Fiber Cement Siding in VA
Contents
In this guide, you'll discover the truth about James Hardie fiber cement siding—one of the most durable and weather-resistant exterior siding materials available today. While many homeowners focus on initial siding costs, this guide explains why fiber cement siding offers unmatched long-term value, curb appeal, and ROI. Made from Portland cement, sand, cellulose fibers, and water,
Hardie board siding resists rot, moisture, pests, fire, and extreme weather. With proper installation and maintenance, it can last 50 to 100 years and deliver over 70% return on investment.
This guide reveals key fiber cement siding performance facts, common installation mistakes, hidden costs, and regional durability concerns that most sales reps never mention.
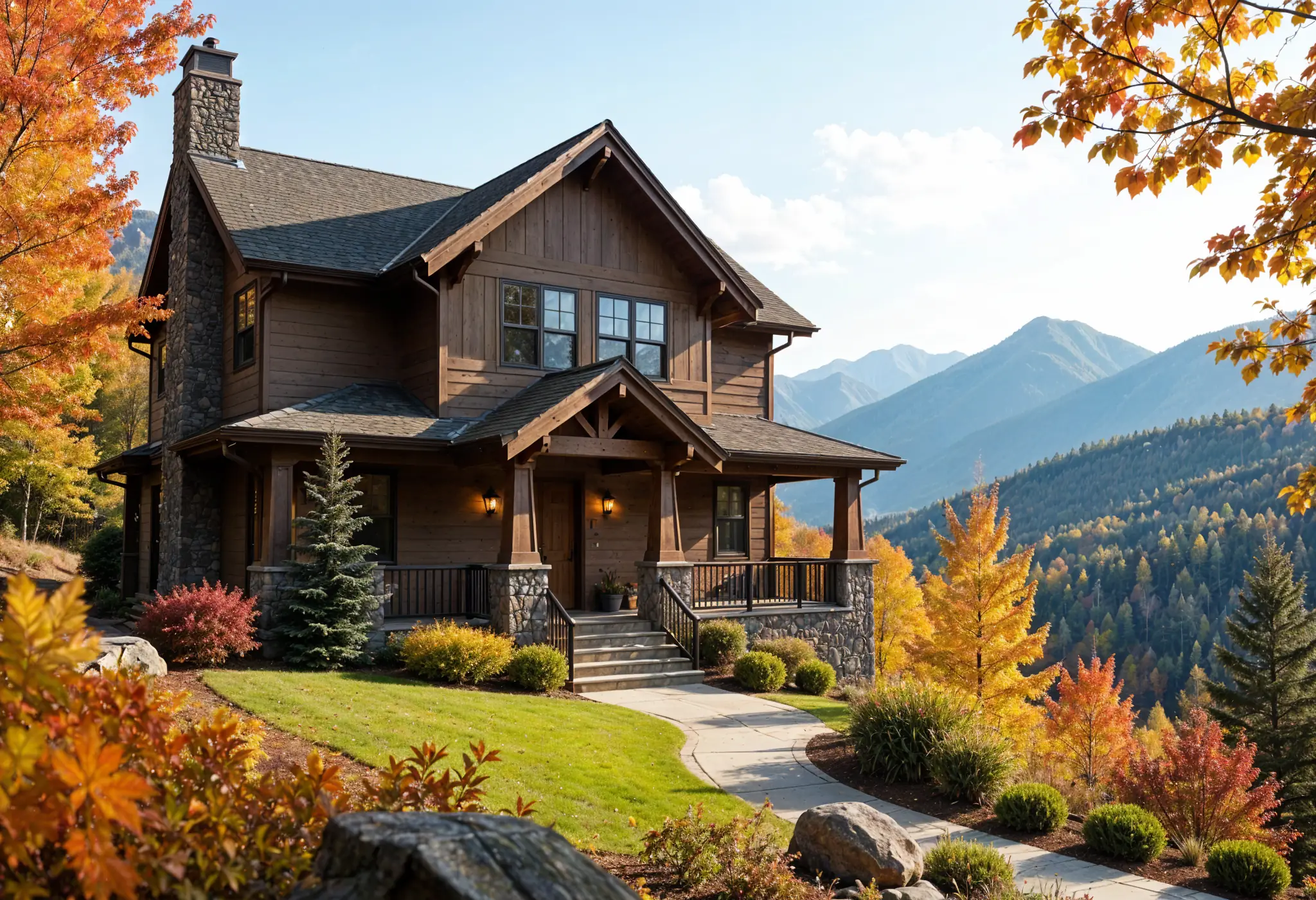
The Truth About Fiber Cement Siding Installation
Proper installation fundamentally determines whether Hardie board siding delivers its promised half-century of protection or fails prematurely. Even seasoned contractors make crucial errors that compromise both appearance and protective function of this otherwise excellent material.
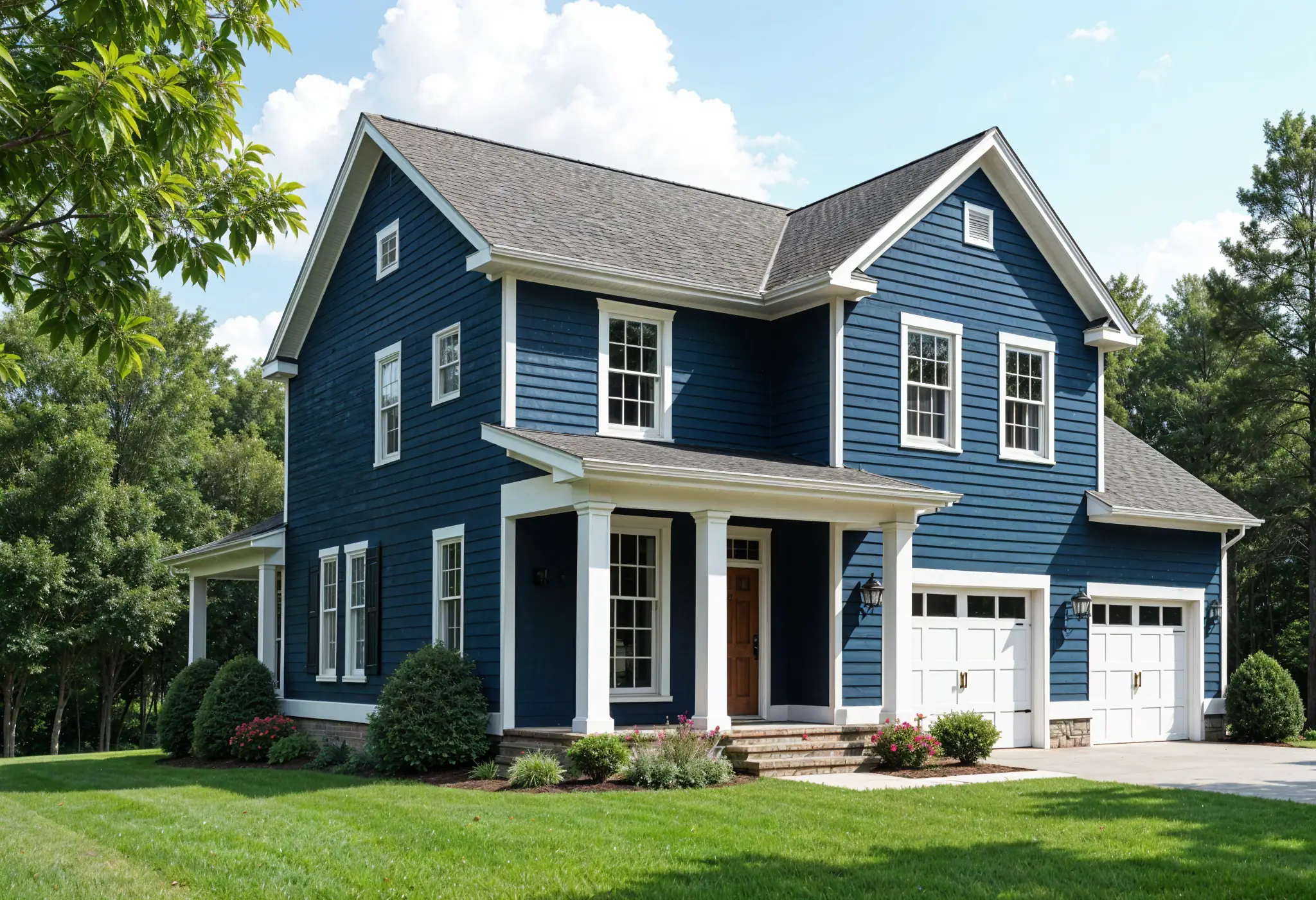
Common installation mistakes even professionals make
Siding failure typically begins with seemingly minor installation errors that create major problems later. Fastening issues rank among the most frequent problems—nails driven too deeply fracture the material, while insufficient penetration leaves panels inadequately secured. Contractors frequently place fasteners incorrectly above the designated nail line, causing panels to rattle during wind events or develop unsightly gaps.
Weather barrier preparation creates another critical vulnerability point. Contractors who skip proper water-resistive barriers or install over uneven surfaces create conditions for moisture penetration and panel misalignment. What appears as a small oversight during installation transforms into structural damage as seasons pass.
Precision cutting and measurement challenges even experienced installers. Gaps between poorly cut boards compromise both visual appeal and weather protection. Many installers mistakenly position siding pieces directly against trim without the manufacturer-required 1/8-inch expansion gap, eventually causing buckling and cracking as materials naturally expand.
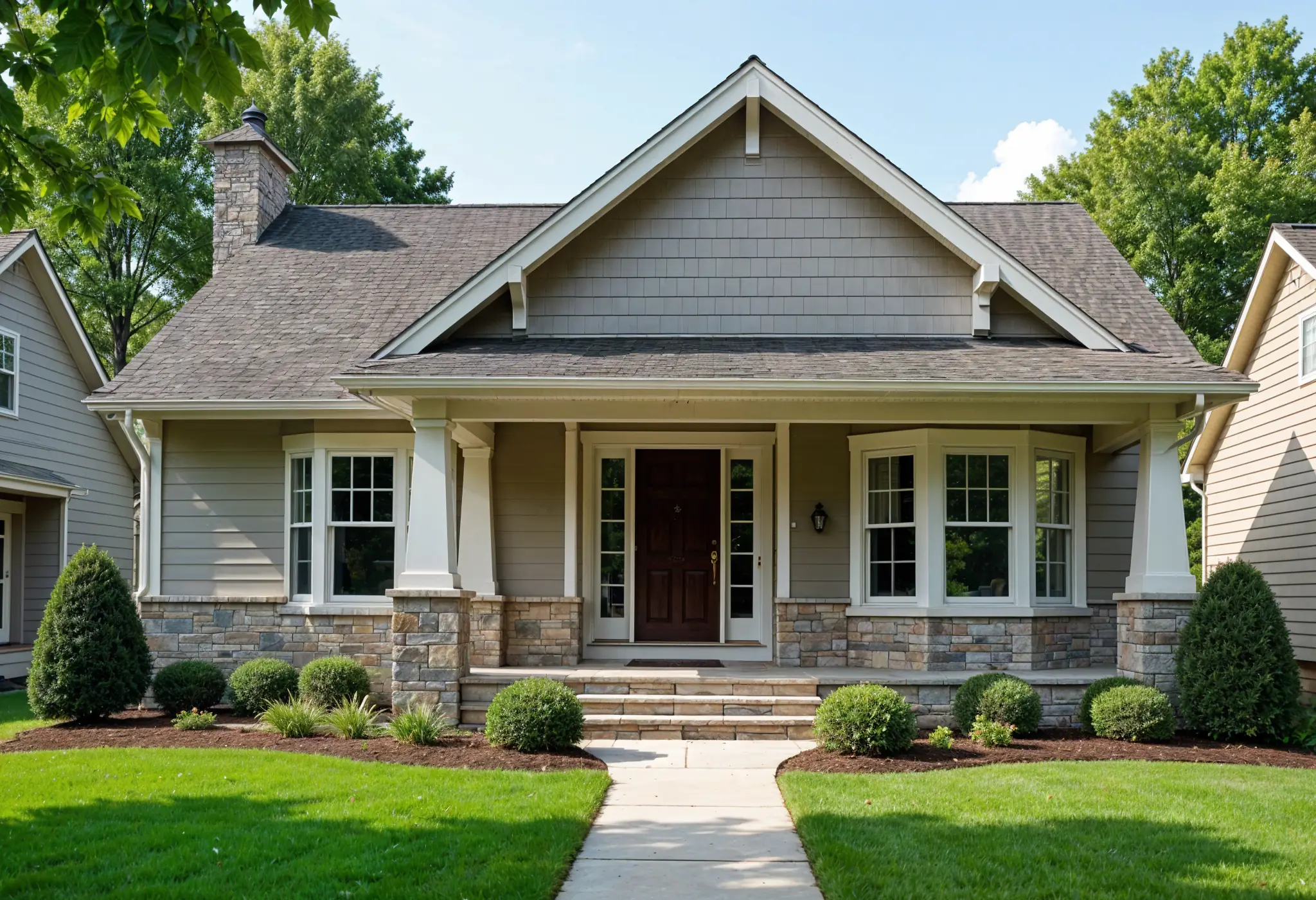
Why proper flashing is more critical than you think
Flashing serves as the unrecognized defender of your home's structural integrity. James Hardie specifically requires 6-inch-wide flashing behind all butt joints that overlaps the course below by 1 inch. This seemingly minor detail prevents water intrusion that ultimately destroys underlying structures.
Penetrations create particularly vulnerable areas requiring meticulous attention. One egregious installation error occurs when contractors position siding breaks directly above dryer vents, essentially creating a channel directing water into interior wall cavities. Similarly, inadequate flashing around windows and doors allows moisture to penetrate behind siding, potentially causing thousands in structural damage before detection.
Properly installed flashing eliminates the need for continuous caulk maintenance at butt joints. However, this significant maintenance advantage materializes only with precise installation techniques—a detail salespeople rarely emphasize.
The hidden costs builders don't mention upfront
Beyond advertised square-foot pricing lie significant additional expenses that impact total project cost. Professional installation for a standard 1,500-square-foot home typically costs approximately $13,000—reflecting the specialized skills required for proper installation rather than simple labor fees.
Permit and inspection requirements add another expense layer that varies substantially by location. Removal and disposal of existing siding materials generate additional fees, particularly if hazardous materials like asbestos exist beneath current siding.
Specialized cutting equipment represents another overlooked expense. Fiber cement requires specific cutting tools to manage dangerous silica dust that poses serious health hazards. These requirements essentially eliminate DIY installation as a viable cost-saving approach for most homeowners.
Most critically, manufacturers void warranties when installation deviates from their detailed specifications. This potential future expense underscores why installation shortcuts ultimately cost substantially more than doing the job correctly initially.
Ensure your siding is installed to the highest standards with James Hardie fiber cement products. Work with a certified team that prioritizes long-term performance and regional requirements. Schedule a professional consultation.
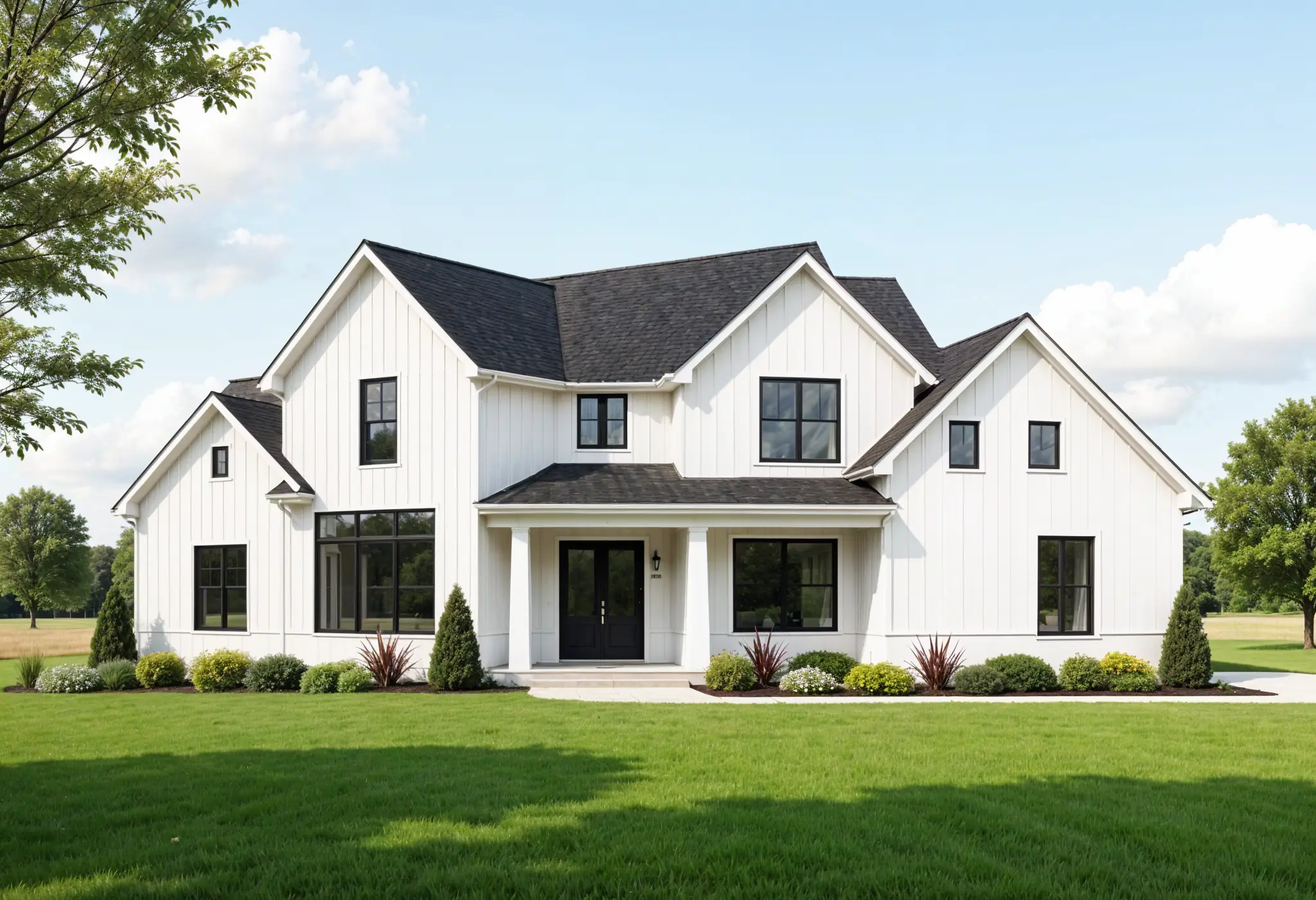
Regional Performance: What Manufacturers Don't Advertise
Fiber cement siding performance varies dramatically across geographic regions—a critical reality manufacturers conveniently omit from glossy brochures and sales presentations. These location-specific differences fundamentally impact installation requirements, durability expectations, and long-term performance outcomes.
How fiber cement really performs in humid coastal areas
Salt air and persistent moisture create unique challenges for coastal homeowners. While marketing materials boldly declare fiber cement siding "waterproof," the actual performance depends entirely on proper installation. High-quality fiber cement maintains its water-repellent properties only when installed with meticulous attention to manufacturer specifications. Premium products incorporate clip installation systems and built-in rainscreens that create essential drainage channels for managing the constant moisture assault coastal homes endure.
Fiber cement's genuine coastal advantage stems from its hurricane-zone certifications rather than basic water resistance. James Hardie products have earned Miami-Dade County Florida approval—among the nation's most demanding extreme weather regulations. Despite these impressive credentials, installation errors remain the primary cause of coastal performance failures. A perfectly engineered product performs poorly when improperly installed.
Cold climate considerations most salespeople ignore
The destructive freeze-thaw cycle creates distinct challenges that sales presentations conveniently minimize. James Hardie developed specialized northern region products (HZ5® products) specifically engineered to resist shrinking, swelling and cracking even after years of punishing wet, freezing conditions. Meanwhile, vinyl siding becomes increasingly brittle as temperatures plummet, making it vulnerable to cracking from ice impacts or even normal seasonal movement.
Fiber cement maintains dimensional stability throughout temperature fluctuations unlike competing materials, preventing the moisture intrusion that breeds mold and rot. This critical benefit materializes only when combined with proper insulation strategies—a crucial detail rarely emphasized during sales presentations focusing on aesthetics rather than functional performance.
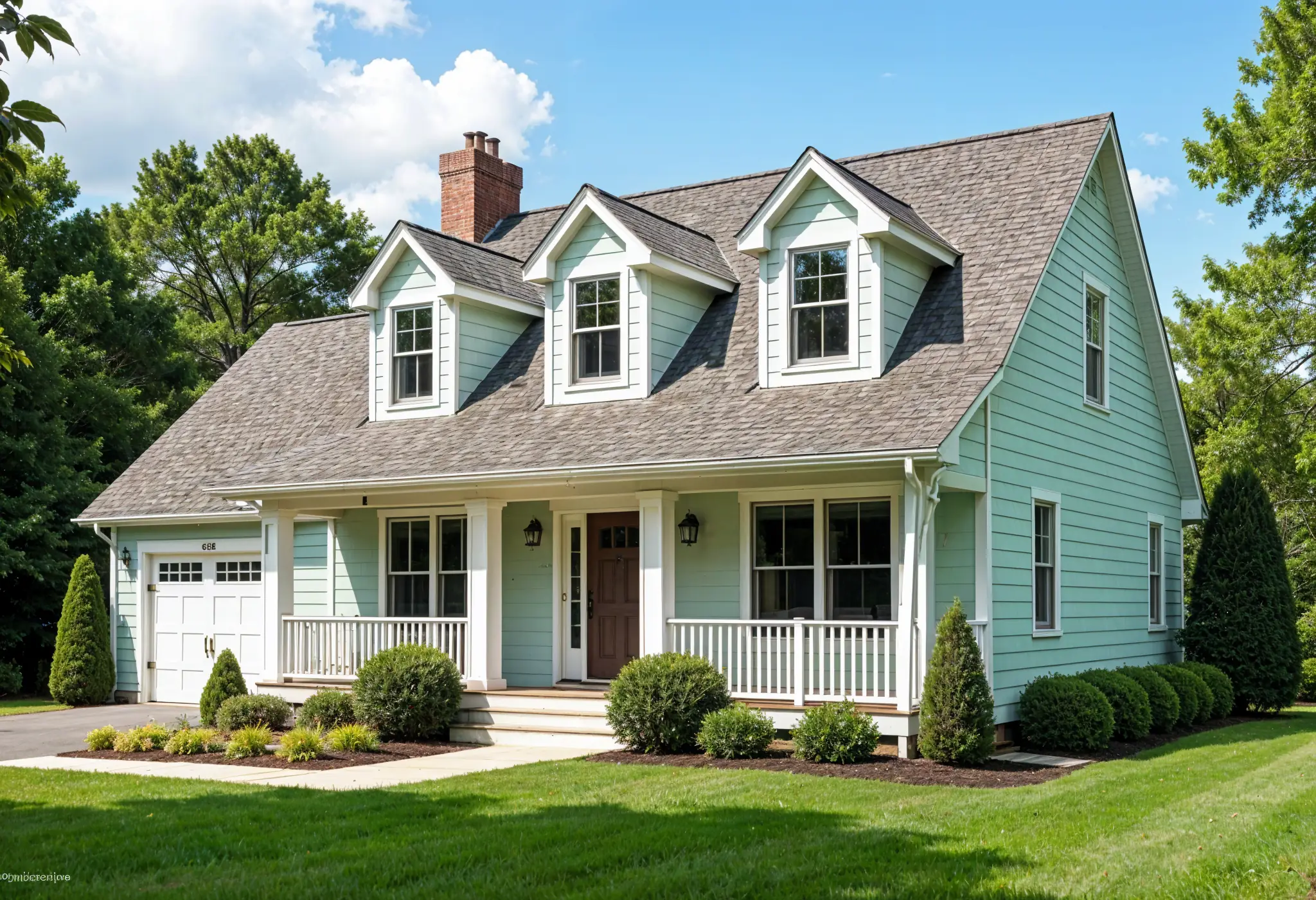
The surprising impact of elevation and sun exposure
Mountain homes face accelerated siding degradation from intense ultraviolet exposure. At higher elevations, the thinner atmosphere allows substantially more UV radiation to reach surfaces, degrading typical siding materials up to 50% faster than identical products at sea level. This intensified solar exposure causes premature fading and structural deterioration unless specifically addressed through material selection.
Reflective heat from energy-efficient windows creates another challenge few homeowners anticipate. Tests demonstrate that Low-E windows concentrate reflected solar radiation, generating temperatures up to 200°F on nearby surfaces. Standard vinyl siding visibly warped after merely one hour at 165°F, while fiber cement withstood localized temperatures between 200°F and 350°F for 24 continuous hours without damage. This thermal stability proves particularly valuable for mountain homes experiencing dramatic daily temperature fluctuations.
Builder's Insights on Fiber Cement Siding Durability
Marketing materials present fiber cement siding as virtually indestructible—yet professional builders witness a more nuanced performance reality daily. This gap between manufacturer promises and actual field performance creates significant implications for homeowners investing in exterior protection.
Real-world lifespan vs. warranty promises
Manufacturer warranties typically provide 30-year coverage for fiber cement siding, yet experienced builders consistently observe these products exceeding warranty periods by decades. Under proper installation and maintenance conditions, fiber cement siding delivers 50-100 year lifespans—more than doubling the protection period covered in standard warranty documents.
This durability-warranty gap reveals a telling industry pattern: manufacturers cautiously promise 30 years while builders regularly witness significantly longer performance. Independent testing confirms fiber cement's capability of maintaining structural integrity for 50-60 years, occasionally reaching the century mark in ideal conditions.
The warranty limitations, however, prove equally significant. James Hardie's 30-year warranty specifically excludes damage resulting from improper installation, structural movement, exceeding wind load ratings, and inadequate maintenance. These exclusions frequently surprise homeowners suddenly facing substantial repair costs for conditions they believed were covered.
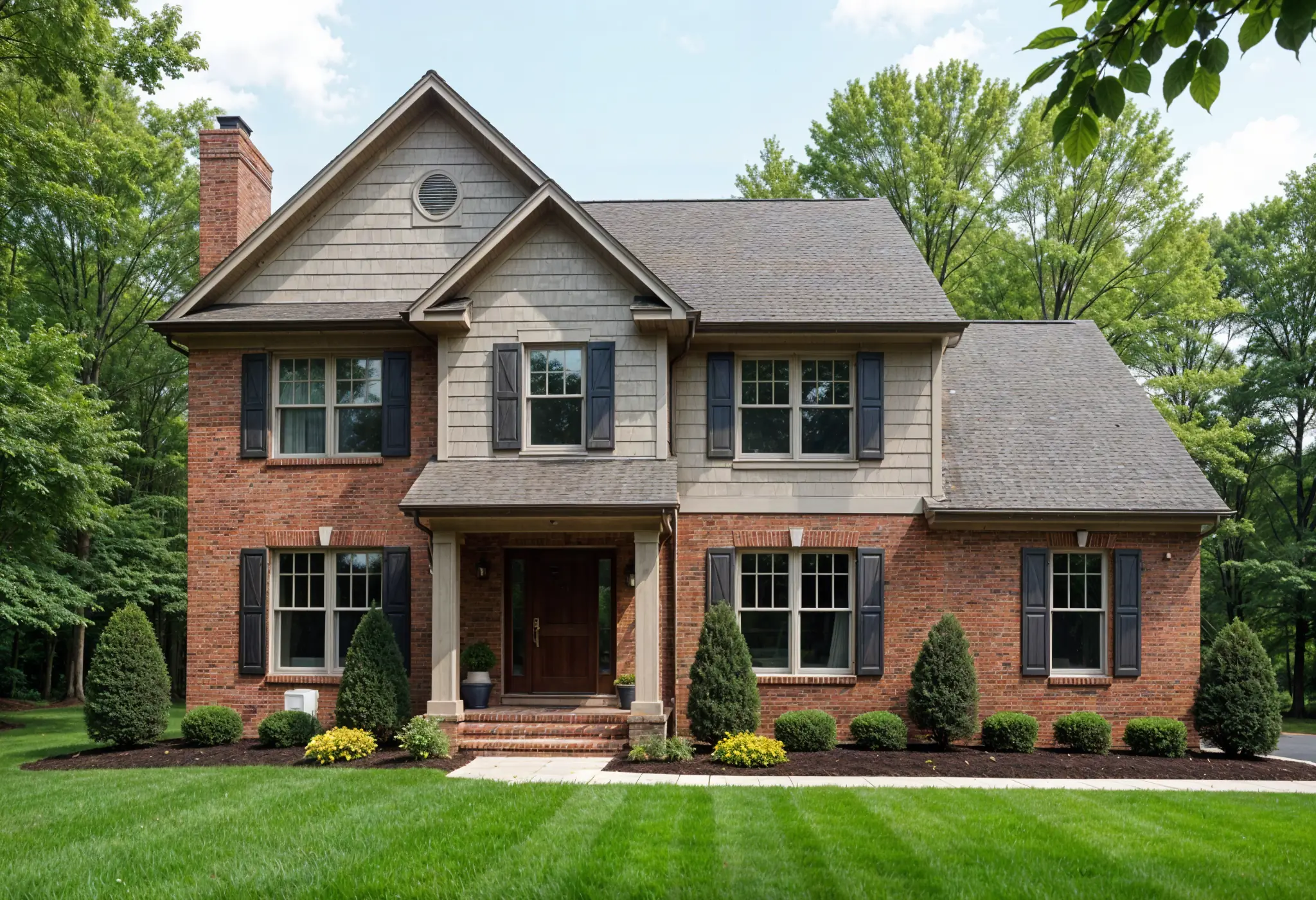
Impact resistance: Marketing claims vs. job site reality
Does fiber cement truly deliver the impact resistance shown in dramatic marketing demonstrations? The answer varies substantially between controlled testing environments and actual construction sites.
Fiber cement undeniably provides superior impact resistance compared to vinyl siding, which dents from relatively minor impacts. Throughout coastal regions, fiber cement earns prestigious HVHZ (High Velocity Hurricane Zone) certifications, including the rigorous Miami-Dade County Florida approval—among the nation's most demanding extreme weather standards.
Job site observations tell a more complex story, however. Fiber cement remains fundamentally brittle and can crack when mishandled during installation or struck by heavy objects after installation. This vulnerability rarely appears in promotional materials featuring carefully controlled demonstrations of baseball impacts against perfectly installed panels.
Temperature conditions further influence real-world impact performance in ways marketing materials conveniently omit. Unlike promotional videos showing impact tests at ideal temperatures, builders observe fiber cement becoming increasingly brittle during freezing conditions. Recognizing this limitation, certain manufacturers produce specialized commercial-grade fiber cement specifically engineered for northern regions, providing enhanced resistance to cold-weather impacts.
Maintenance Secrets from Professional Builders
Though fiber cement siding demands substantially less maintenance than wood alternatives, specific care routines maximize its decades-long performance potential. Professional builders employ maintenance strategies far more sophisticated than the basic guidelines manufacturers include with their products.
The cleaning routine manufacturers don't emphasize enough
Annual or semi-annual cleaning serves as critical preventive maintenance rather than merely aesthetic care. Professional builders recognize that accumulated dirt, mold spores, and environmental contaminants gradually compromise both appearance and structural integrity when left undisturbed on siding surfaces.
Cleaning technique significantly impacts long-term performance. Rather than pressure washers (which most manufacturers quietly discourage), experienced builders recommend:
- Using garden hoses with standard pressure and soft-bristle brushes
- Working methodically from top to bottom in small sections to prevent streaking
- Applying mild detergent solutions only for stubborn stains or biological growth
"Most homeowners damage their siding using pressure washers exceeding 1,500 psi or standing within six feet of the surface," notes one experienced builder. "This practice erodes the protective finish and potentially voids the manufacturer's warranty."
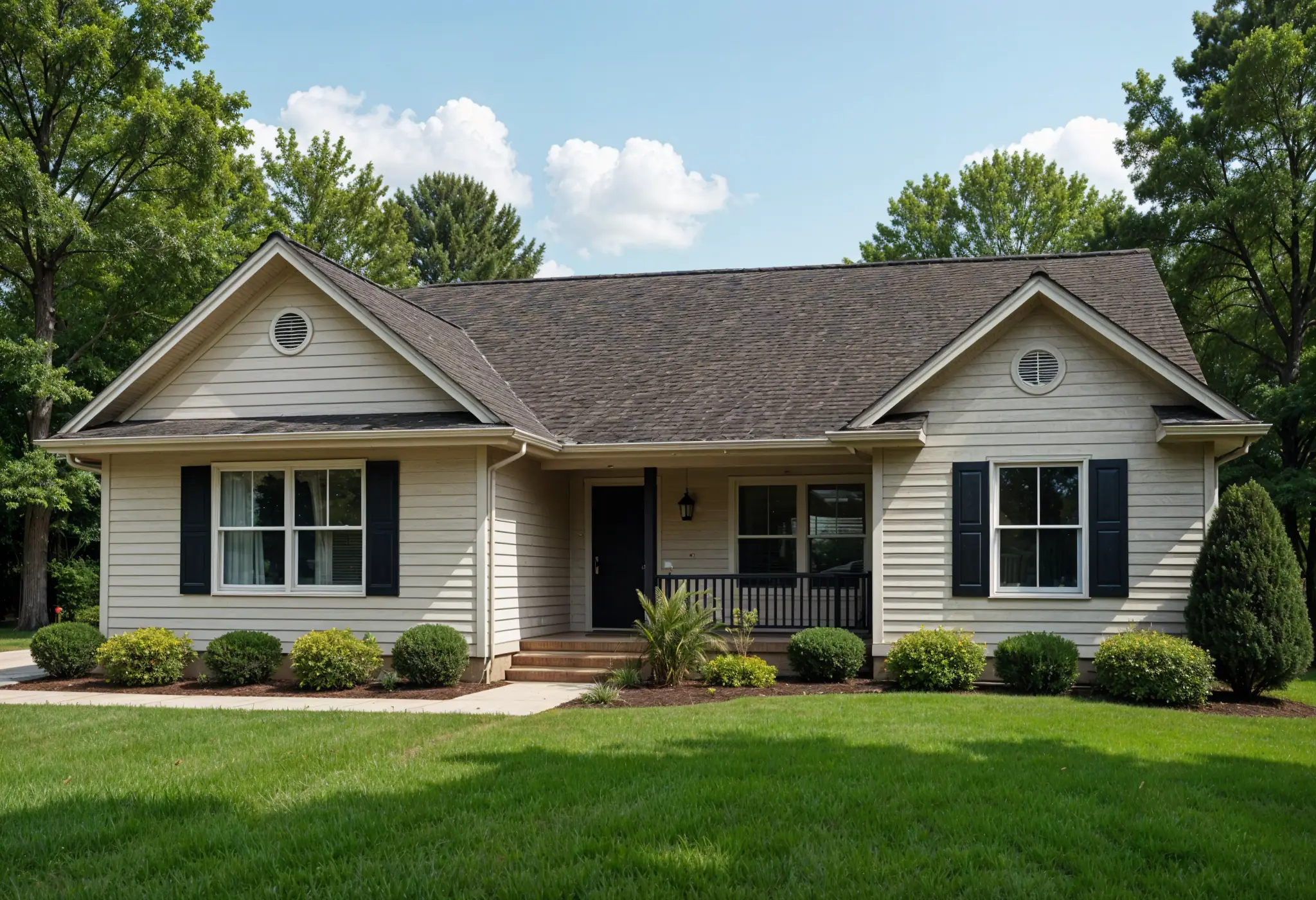
When to repair vs. when to replace damaged sections
Professional builders evaluate several key factors when determining repair versus replacement strategies. Repair typically offers the most cost-effective solution when:
- Damage affects only one or two isolated panels
- Issues involve minor cracks, chips, or small mold patches
- The underlying structural elements remain completely sound
Replacement becomes necessary under specific conditions:
- Damage extends across multiple panels or large sections
- The siding has exceeded 15 years with developing problems
- Structural issues exist beneath the siding surface
- Energy consumption has increased, indicating insulation degradation
For minor repairs, builders apply cementitious patching compounds specifically formulated for fiber cement, followed by proper paint touch-ups that maintain critical moisture resistance properties.
Choose siding solutions engineered for your climate—HZ5® for cold regions, with proven resistance to moisture, pests, and structural deterioration. Explore our James Hardie siding services.
Painting cycles: What the warranty fine print doesn't highlight
While manufacturers boldly advertise 30-50 year structural warranties, the fine print reveals a substantially different reality regarding finish durability. Factory-applied finishes typically require repainting after 10-15 years, while field-painted surfaces often demand attention within 7-10 years. Since proper painting constitutes essential moisture protection, this maintenance essentially becomes mandatory rather than optional.
The warranty implications around painting remain substantial yet understated. Manufacturers rarely emphasize that using incorrect paint formulations automatically voids warranty coverage. Professional builders strictly follow these guidelines:
- Using only 100% acrylic latex paints specifically formulated for fiber cement
- Avoiding all stains, oil-based, and alkyd paints without exception
- Performing thorough surface preparation and cleaning before applying new paint
These seemingly minor painting specifications carry major warranty implications—manufacturers routinely exclude coverage for damage resulting from improper maintenance practices, transforming technical details into financially significant considerations for long-term performance.
Conclusion
Fiber cement siding, especially James Hardie siding, remains one of the most durable and weather-resistant exterior materials available for homeowners. When installed correctly and maintained properly, it offers long-term protection, curb appeal, and a lifespan of 50–100 years. For cold climates, James Hardie’s HZ5® products are engineered to withstand freeze-thaw cycles, while in coastal areas, moisture control and hurricane-rated systems are essential. These regional factors directly impact siding performance and must guide product selection.
Routine fiber cement siding maintenance—such as soft-wash cleaning, timely repairs, and repainting with approved acrylic coatings—is critical to preserving structural integrity and protecting your investment. With proper care, this siding type consistently outperforms manufacturer warranties. Use this guide to choose the right fiber cement siding, avoid costly installation errors, and ensure your home stays protected against rot, moisture damage, pests, and extreme temperatures for decades.
Protect your home with expertly installed fiber cement siding that performs beyond manufacturer warranties. Get a detailed estimate and installation plan tailored to your property. Request your personalized quote.
FAQs
Q1. What are the main advantages of fiber cement siding? Fiber cement siding offers exceptional durability, with a lifespan of 50-100 years when properly maintained. It's resistant to rot, pests, moisture, and fire, making it a long-lasting and protective option for homes. Additionally, it provides excellent curb appeal, low maintenance requirements, and is available in various styles including wood grain texture and smooth finish options.
Q2. How does fiber cement siding perform in different climates? Fiber cement siding performs well in various climates, but its effectiveness can vary. In humid coastal areas, proper installation is crucial for moisture management. For cold climates, specific product variants like James Hardie's HZ5® are recommended to resist freezing conditions. The material's weather resistance and fade resistance make it suitable for diverse environments.
Q3. What are some common installation mistakes to avoid with fiber cement siding? Common installation errors include inadequate fastening, improper surface preparation, and inaccurate measurements. It's crucial to follow manufacturer guidelines for fastening, flashing, and allowing proper gaps for expansion to ensure optimal performance. Proper caulking and sealing are also essential for long-lasting beauty and protection.
Q4. How often does fiber cement siding need to be painted? Factory-applied finishes on fiber cement siding, such as James Hardie's ColorPlus Technology, typically require repainting after 10-15 years. Field-painted surfaces may need attention sooner. Regular maintenance and proper painting are essential for long-term moisture protection and appearance.
Q5. What maintenance is required for fiber cement siding? Maintenance for fiber cement siding includes annual cleaning with a garden hose and soft-bristle brush, avoiding pressure washers. Inspect regularly for damage, make timely repairs, and follow proper painting cycles using 100% acrylic latex paints designed for fiber cement. This low maintenance approach helps maintain the siding's aesthetic appeal and protective properties.