Fiber Cement vs Vinyl Siding
Contents
In this comprehensive guide, we compare fiber cement siding and vinyl siding to help you make an informed decision for your home's exterior. Vinyl remains the most popular choice, lasting over 20 years with installation costs starting at $6–$8 per square foot. Fiber cement, while more expensive at $9–$12 per square foot installed, offers unmatched durability of 30–50 years. Made from Portland cement, sand, and cellulose fibers, fiber cement is five times thicker than vinyl, non-combustible, and more eco-friendly—features that can reduce insurance premiums and appeal to green-conscious homeowners.
You'll learn how these materials stack up in durability, maintenance, cost, aesthetics, and climate performance.
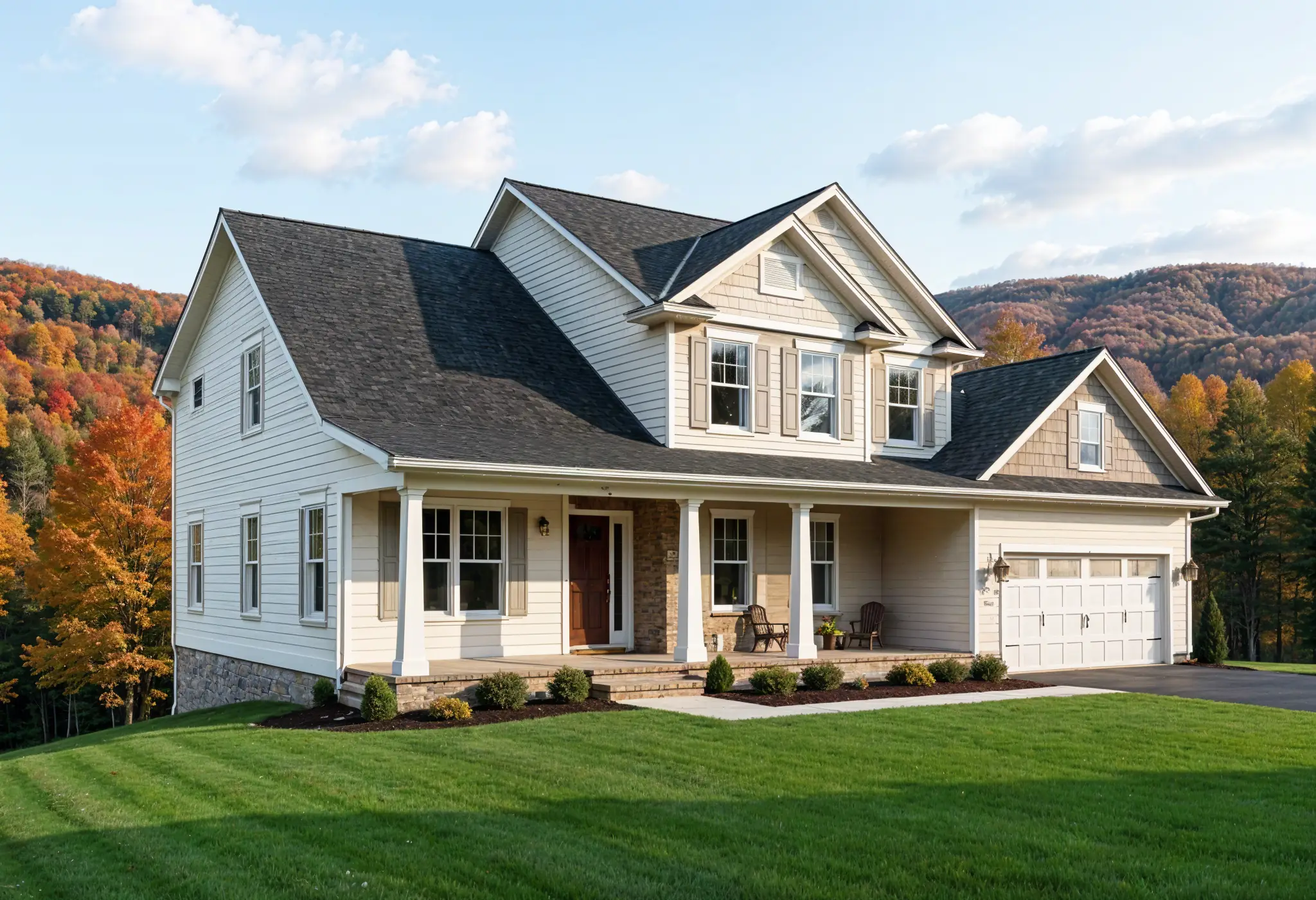
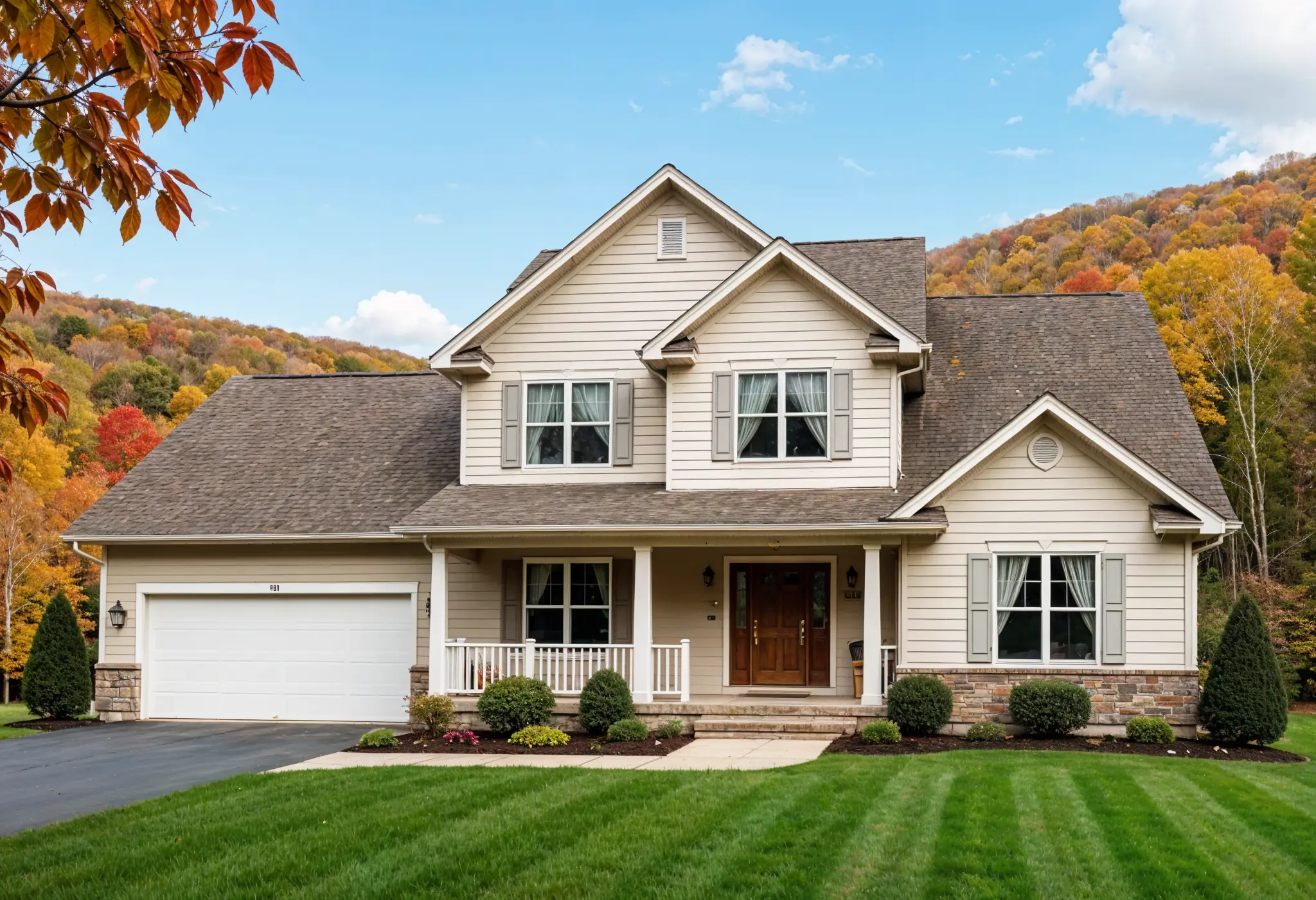
What Do You Want From Your Siding?
Selecting the perfect siding involves balancing several key factors beyond initial appearance. Before making your decision between fiber cement siding vs vinyl, consider what you truly need from this crucial exterior component.
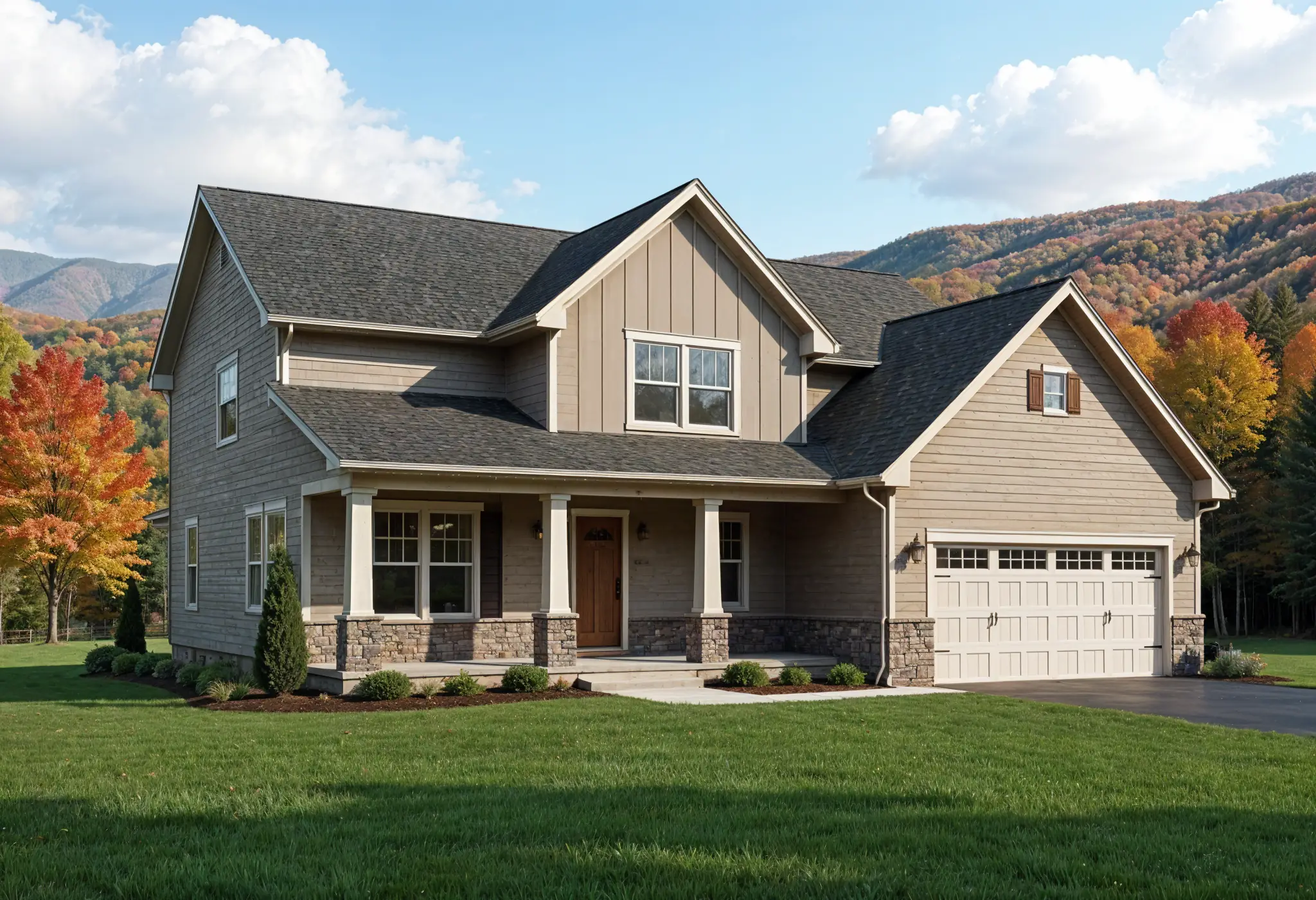
1. Durability vs affordability
The relationship between longevity and cost deserves careful consideration. Vinyl siding remains one of the most budget-friendly options, offering 20-40 years of service when properly maintained. For many homeowners, this represents an excellent value proposition with minimal upkeep requirements—typically just occasional washing to maintain its appearance.
Fiber cement siding, though initially more expensive, delivers exceptional durability with a lifespan often exceeding 50 years. This remarkable longevity comes with significant benefits:
- Resistance to termites and pests
- Superior performance against extreme weather conditions
- Non-combustible properties that can reduce insurance costs
James Hardie fiber cement siding, often referred to as Hardiplank siding, stands out for its ability to withstand both extreme heat and cold, making it particularly suitable for regions with diverse weather patterns. Although it requires a higher upfront cost, its long-term value often justifies the investment, especially when you consider reduced maintenance and replacement expenses over decades.
2. Aesthetic goals and curb appeal
Your siding choice dramatically influences your home's visual impact. More than 65% of buyers cite curb appeal as the most important aspect of a home's exterior design. Consequently, selecting the right siding material and design is crucial for creating an attractive, cohesive look.
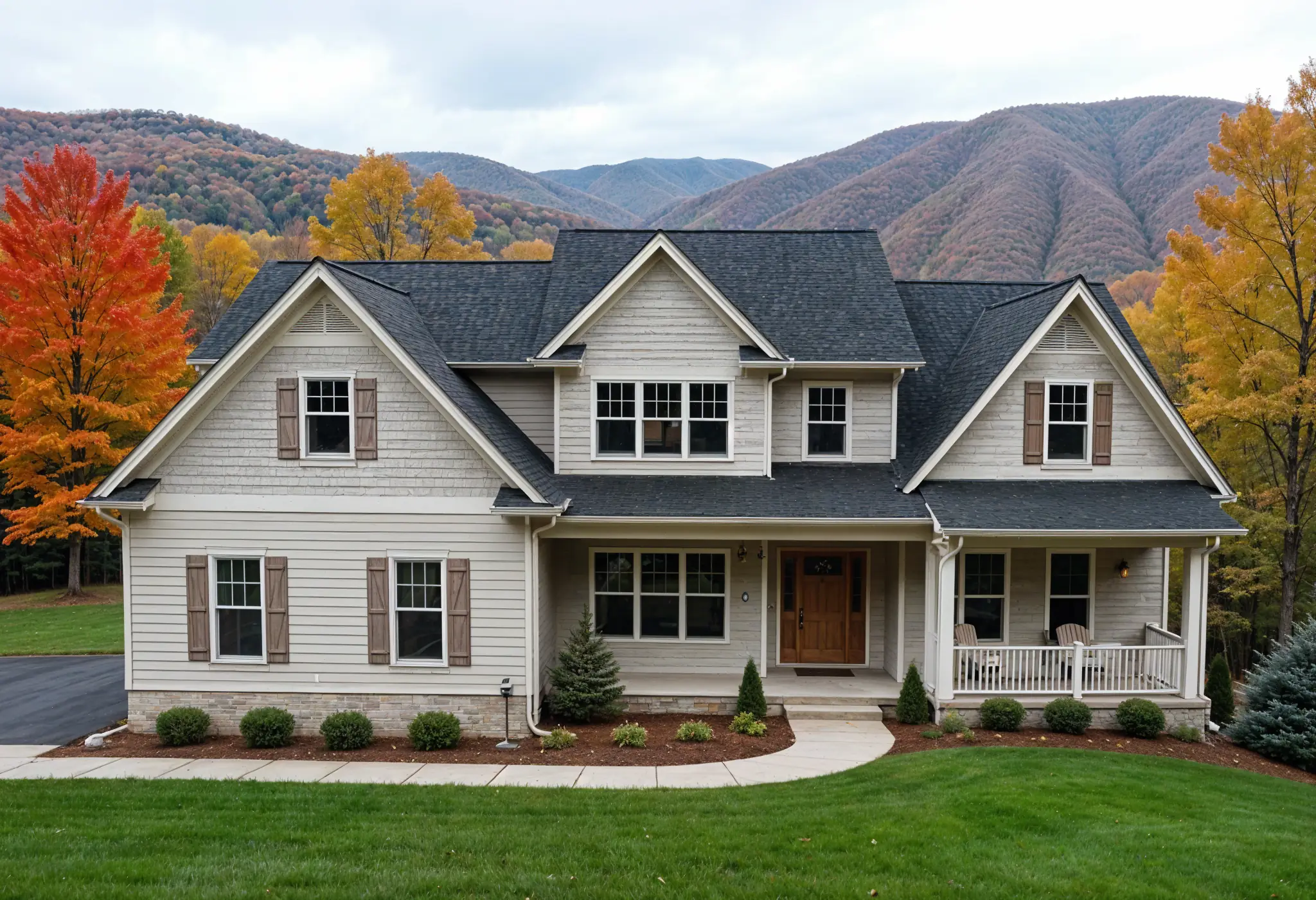
Fiber cement siding offers the versatility to mimic the appearance of wood or masonry while requiring minimal maintenance. This adaptability allows you to achieve your desired aesthetic without compromising on performance. The wood-like appearance of fiber cement siding is particularly appealing to homeowners seeking a traditional look with modern durability.
Vinyl siding provides numerous style and color options, though it may lack the natural aesthetic of other materials and can fade over time. Nevertheless, its affordability and variety make it a popular choice for homeowners seeking to enhance curb appeal on a budget. When considering vinyl siding comparison, it's important to note that while it offers good customization options, it may not match the texture options and paint retention of fiber cement.
3. Energy efficiency and insulation needs
Proper insulation significantly impacts both comfort and utility bills. Insulated siding improved measured airtightness by more than 9.5% in one study, with normalized utility bill data showing an 8% reduction in energy consumed during the heating season.
When evaluating insulation performance, consider:
Fiber cement siding provides excellent thermal resistance through its dense composition. However, for optimal energy efficiency, additional insulation layers may be necessary.
Insulated vinyl siding features foam backing that boosts its R-value, potentially reducing energy costs by up to 20% according to the U.S. Department of Energy. Furthermore, its integrated design makes installation straightforward.
The climate in your region should influence your choice. Homes in colder regions benefit from siding with higher insulation values to maintain indoor temperatures regardless of external conditions.
Need expert guidance on siding selection? Schedule a complimentary consultation with My Modern Renovations to evaluate the best material for your home based on climate, longevity, and value. Visit mymodernrenovations.com
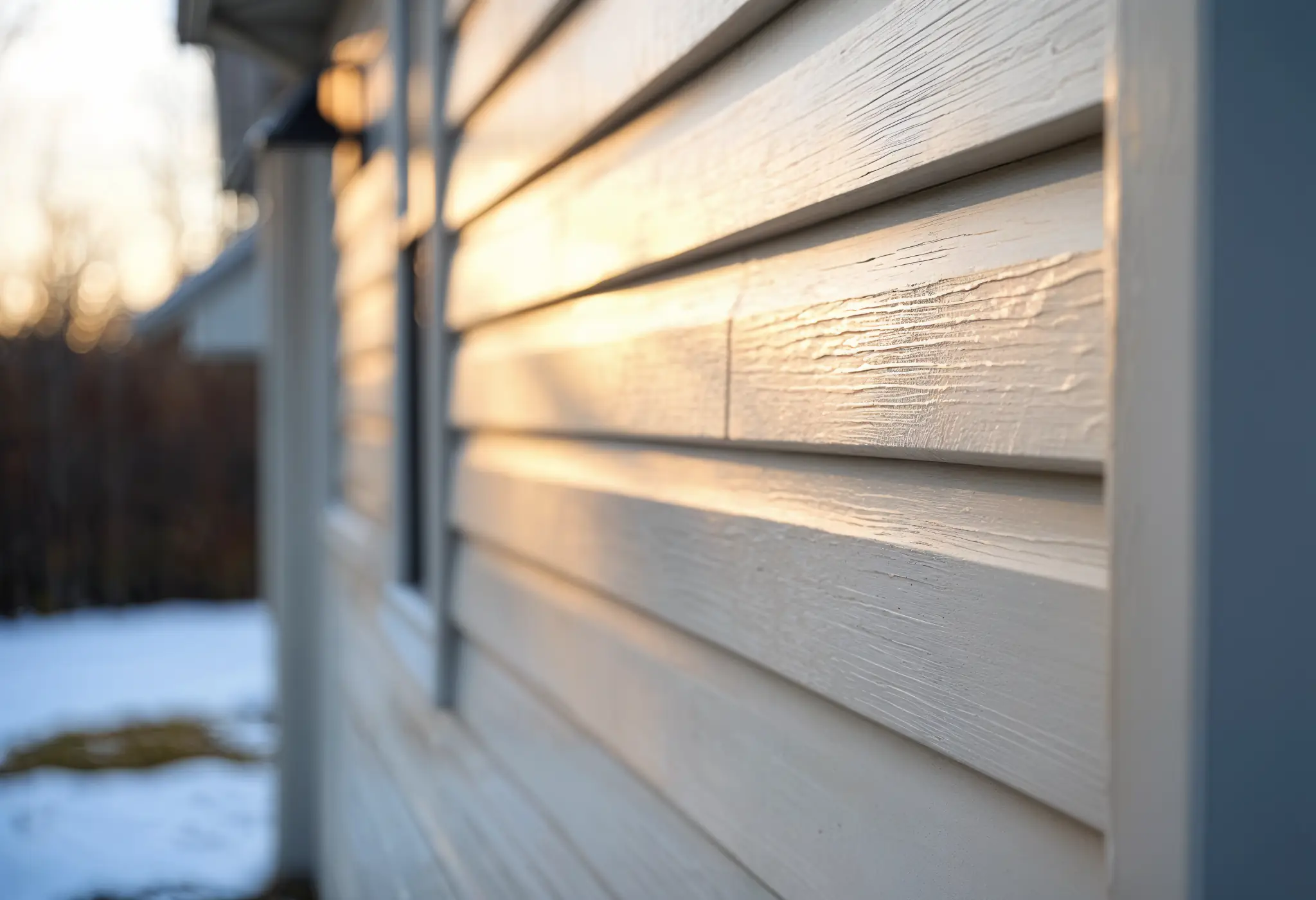
Comparing Performance: Fiber Cement vs Vinyl Siding
When analyzing real-world performance, the differences between fiber cement and vinyl siding become crystal clear. From basic weather protection to specific climate adaptations, these materials behave quite differently under pressure. This durability comparison is crucial for homeowners making long-term decisions about their property.
1. Lifespan and weather resistance
The longevity gap between these materials is substantial. Fiber cement siding lasts 50-100 years with proper maintenance, whereas vinyl typically performs for 20-40 years. This dramatic difference stems from their fundamental composition and highlights the importance of considering siding material lifespan in your decision-making process.
Fiber cement excels in weather resistance due to its dense, non-porous structure. It doesn't warp or trap water, making it ideal for homes in variable climates. Its moisture resistance prevents rot and structural damage even after complete water saturation for seven days. This rot resistance is a significant advantage over other siding materials.
Vinyl siding, conversely, performs adequately in moderate conditions but becomes brittle in extreme cold and can experience warping under high heat. This vulnerability makes it less reliable for regions experiencing severe temperature fluctuations. However, vinyl siding maintenance is generally less demanding, which is an important consideration for some homeowners.
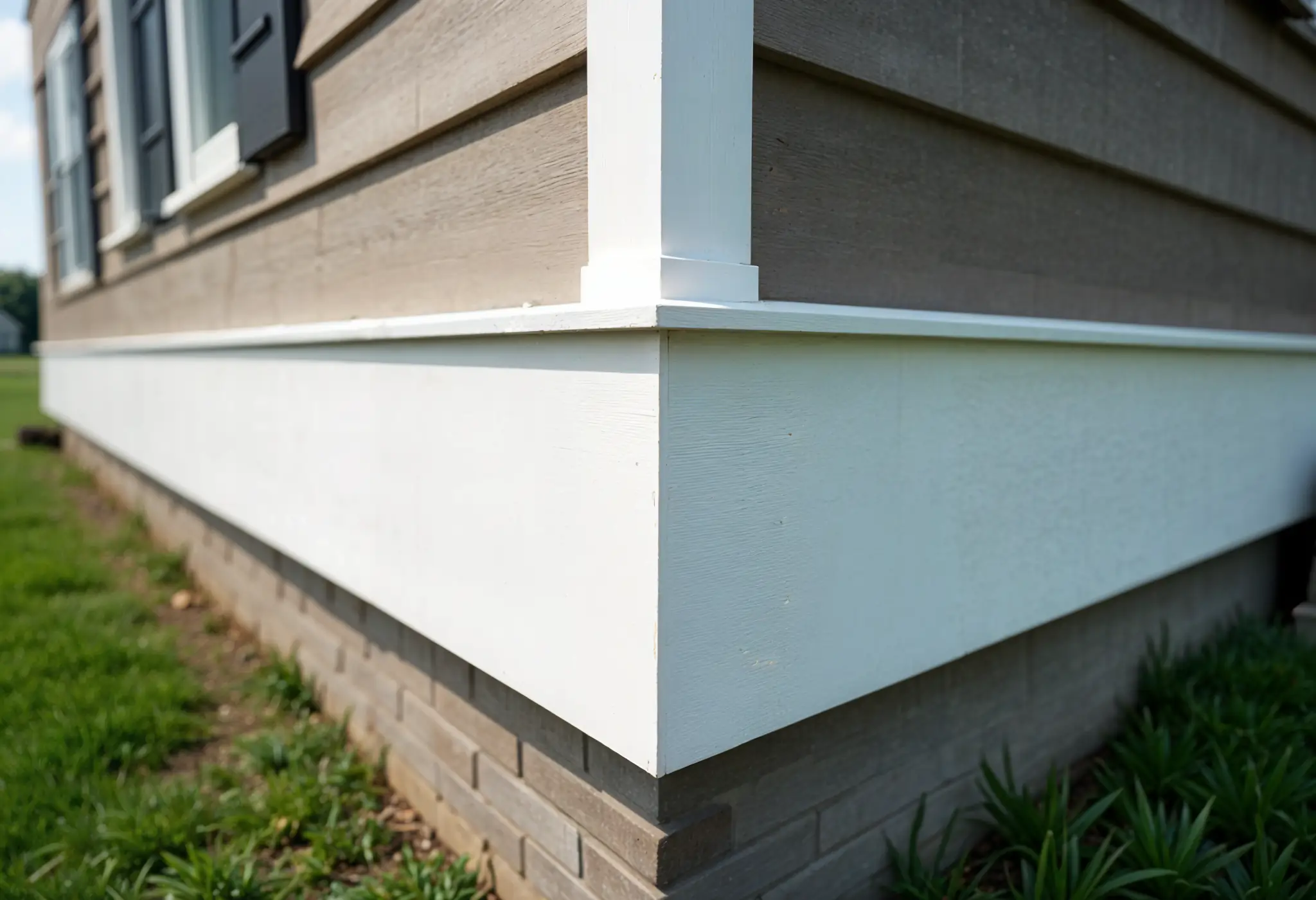
2. Fire safety and environmental impact
Fire safety represents perhaps the starkest contrast between these materials. Fiber cement siding achieves a Class 1(A) fire spread rating—the highest possible. It won't ignite or release toxic fumes during a fire, potentially saving lives and property.
Vinyl siding, made primarily from PVC, melts when exposed to high heat. This characteristic makes it particularly problematic for homes in fire-prone areas, as it can actually contribute to flame spread rather than contain it.
From an environmental perspective, the materials diverge significantly. Fiber cement contains recyclable components like cement, sand, and cellulose fibers. Vinyl siding's production releases harmful VOCs and greenhouse gasses, including DEHP, and its petroleum-based composition means it's non-biodegradable.
3. Siding for cold climates like West Virginia
For cold-climate regions like West Virginia, siding performance during freeze-thaw cycles becomes crucial. Fiber cement siding maintains its structural integrity throughout these cycles, neither expanding nor contracting significantly as temperatures fluctuate.
James Hardie fiber cement siding specifically engineers products for cold climates through their HardieZone® System—with HZ5® products designed to resist cracking, shrinking, and swelling caused by freezing conditions.
In contrast, vinyl can become increasingly brittle as temperatures drop below zero for extended periods. This brittleness creates vulnerability to cracking and subsequent moisture infiltration, particularly problematic during spring thaws.
Namely for West Virginia homes, fiber cement's resistance to moisture infiltration prevents mold development and internal water damage, critical in mountainous areas where melting snow creates persistent moisture challenges.
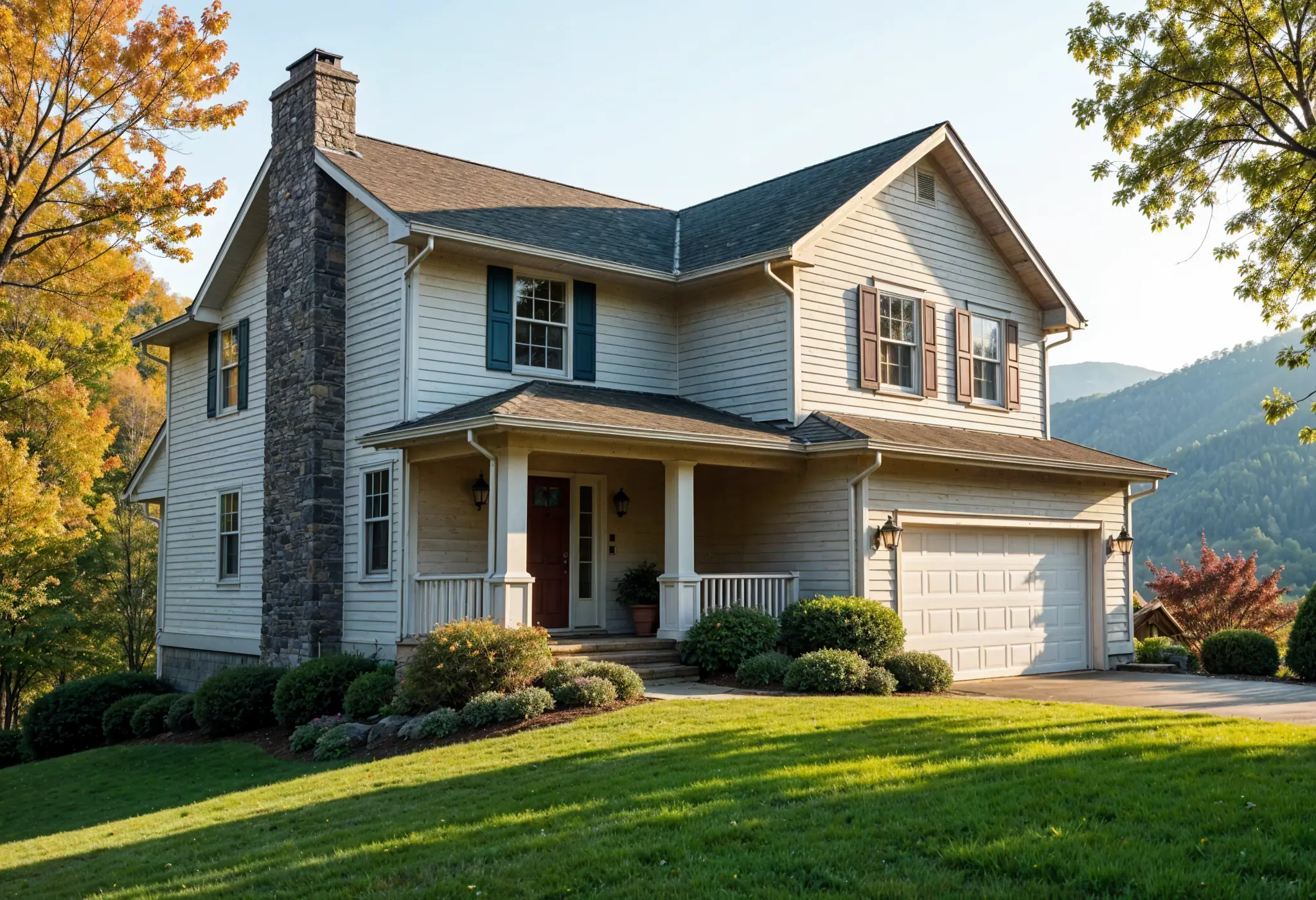
Installation and Upkeep: What to Expect
Beyond material selection, understanding the practical aspects of installation and maintenance ensures realistic expectations for your siding project. The contrast between fiber cement and vinyl extends to how they're installed and maintained over decades of performance.
1. Installation complexity and labor costs
The weight difference between these materials significantly impacts installation. Fiber cement siding weighs approximately 150 pounds per 50 square feet, making it five times heavier than vinyl, which typically weighs only 30-35 pounds per square foot. This substantial weight difference creates cascading effects on your project.
Fiber cement installation requires specialized tools, professional expertise, and safety precautions for handling crystalline silica. As a result, it's never considered a DIY project, even for experienced homeowners. Moreover, its installation requires additional steps like caulking and painting that vinyl doesn't need.
These factors translate directly to your bottom line. Labor costs for fiber cement typically range between $4.00-$8.00 per square foot, whereas vinyl installation runs substantially lower at $2.00-$5.00 per square foot. When considering the cost of cement board siding vs vinyl, it's important to factor in these installation differences.
2. Maintenance frequency and repainting needs
Maintenance requirements create another sharp distinction between these materials. Vinyl siding stands out for its minimal upkeep - simply hosing it down occasionally keeps it looking fresh. Indeed, this remains one of vinyl's biggest selling points and a key aspect of vinyl siding maintenance.
Fiber cement, despite being lower-maintenance than wood, requires annual cleaning and inspection. Subsequently, you'll need to repaint it every 10-15 years as the finish fades. Additionally, annual caulk inspections are necessary to prevent moisture problems. While this might be seen as one of the disadvantages of fiber cement siding, many homeowners find the trade-off in durability and appearance worthwhile.
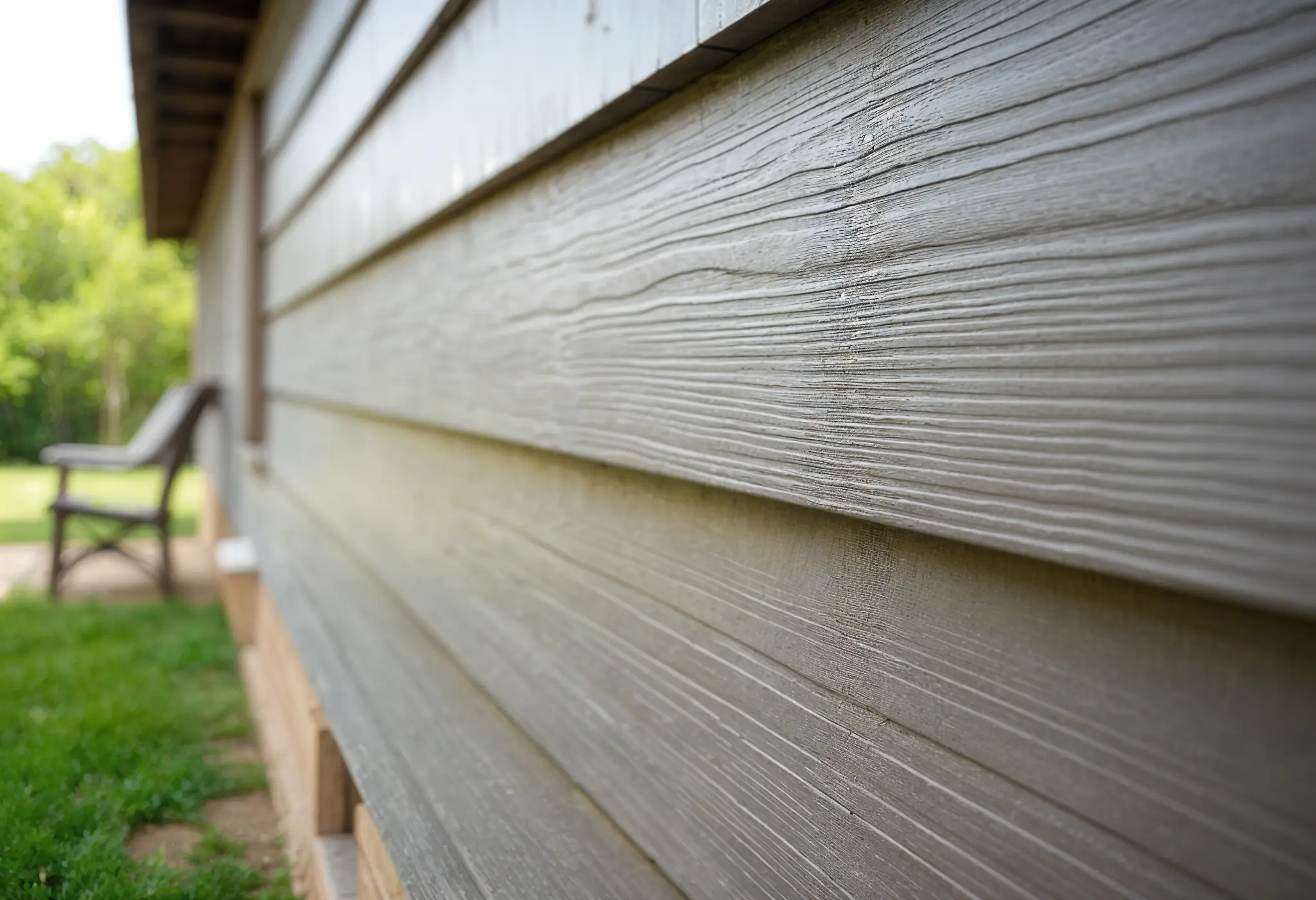
3. Tips for choosing the right installer
Selecting the right contractor dramatically affects your siding's performance. Consider these essential criteria:
- Choose local specialists who understand regional climate challenges
- Verify proper licensing, insurance coverage, and workmanship warranties
- Request references from recent customers with similar siding projects
- Confirm they're certified by your siding manufacturer to protect warranties
Remember that the most affordable bid isn't always the best value. Improper installation of either material can void warranties and create expensive problems down the road. For James Hardie fiber cement, specifically seek contractors recognized through their ALLIANCE program.
Enhance your home’s exterior with precision-installed siding. Partner with My Modern Renovations for high-performance vinyl or fiber cement solutions, tailored to withstand West Virginia’s climate while boosting long-term value. Request your estimate.
Making the Right Choice for Your Home
The final choice between these competing materials ultimately rests on your specific circumstances, priorities, and location. After examining performance and installation considerations, it's time to make your selection.
1. Is fiber cement siding better than vinyl for your region?
Your geographical location plays a decisive role in siding selection. For homes in areas experiencing extreme weather conditions, fiber cement's superior resistance to hurricane-force winds, blistering heat, humidity, and freezing temperatures makes it the optimal choice.
Alternatively, in milder climates, vinyl siding performs adequately with fewer weather-related concerns. Homeowners in West Virginia and similar regions with temperature fluctuations should note that fiber cement maintains its structural integrity throughout freeze-thaw cycles, unlike vinyl which can become brittle in extreme cold.
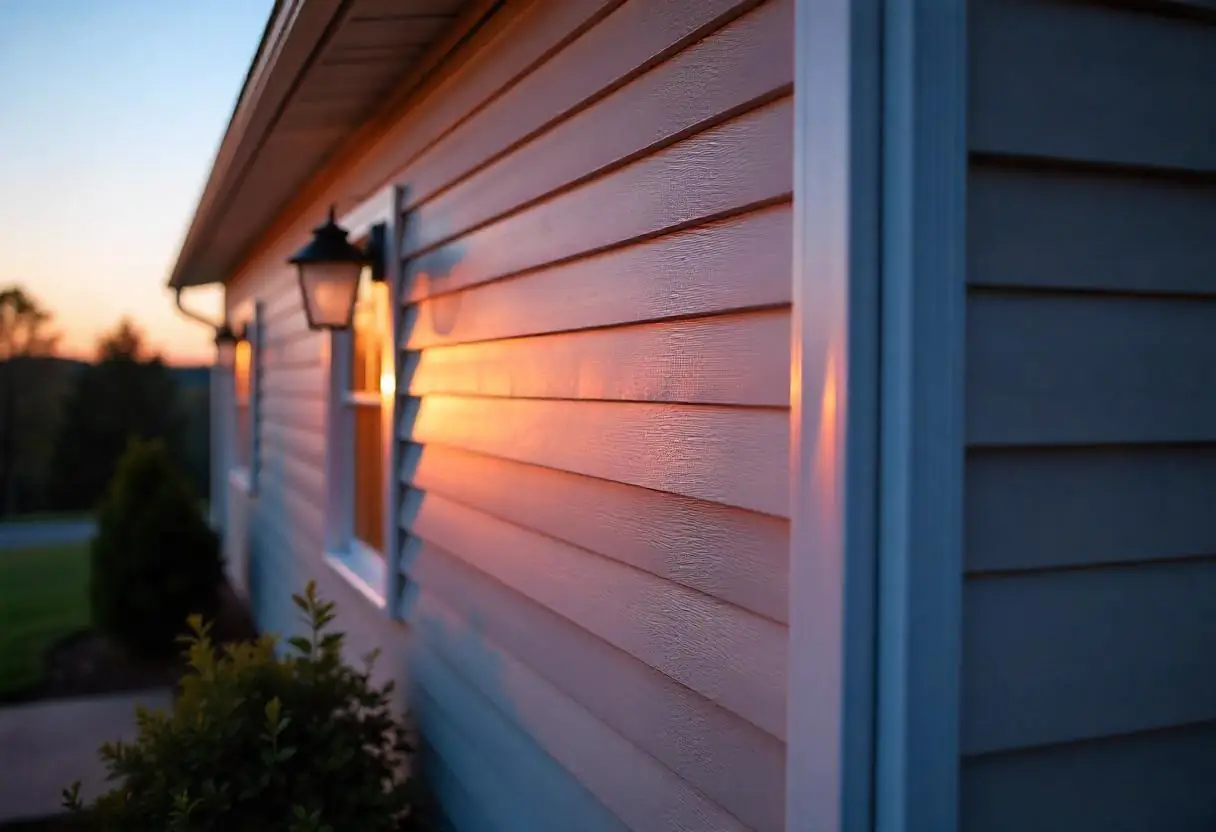
2. James Hardie fiber cement siding vs vinyl: brand insights
James Hardie products stand out in the fiber cement category for their proprietary features. Their siding is engineered specifically for different climate zones through their HardieZone® System.
In side-by-side comparisons, James Hardie offers impressive durability advantages:
- Lifetime value exceeding typical repair cycles
- Non-combustible composition versus vinyl's vulnerability to fire
- Superior impact resistance against hail and debris
3. How siding choice affects home value and insurance
Fiber cement significantly outperforms vinyl in return on investment. According to the 2023 Remodeling Cost vs. Value Report, fiber cement siding adds approximately $17,129 to home value (88.5% ROI) compared to vinyl's $15,490. This difference in resale value of different siding types can be a crucial factor for homeowners planning to sell in the future.
Importantly, insurance companies typically view fiber cement more favorably because of its fire resistance. Many homeowners see reduced insurance premiums after installing fiber cement siding, which contributes to its long-term cost-effectiveness.
4. Final checklist before deciding
Before making your final decision, consider these crucial factors:
- Long-term outlook: Will you stay in your home for decades, making fiber cement's 50+ year lifespan worthwhile?
- Budget constraints: Can you afford the 30-50% higher initial investment for fiber cement?
- Aesthetic priorities: Do you value the authentic wood appearance that fiber cement provides?
- Resale timing: For immediate resale, vinyl might suffice; for long-term value, fiber cement offers superior returns
For most homeowners seeking the optimal balance between durability, aesthetics, and long-term value, fiber cement emerges as the superior option—provided the budget accommodates its higher initial cost.
Conclusion
Choosing between fiber cement and vinyl siding is a major investment in your home's future. Vinyl is affordable and lasts 20–40 years, but fiber cement offers unmatched durability, with a lifespan of 50+ years. While the upfront cost is higher, fiber cement provides superior weather resistance, fire safety, and long-term value. It performs exceptionally well in regions like West Virginia, where extreme weather and freeze-thaw cycles are common. Its fire-resistant makeup may lower insurance premiums, and it delivers a strong return on investment—up to 88.5% according to recent data. For homeowners focused on longevity, durability, and resale value, fiber cement is the smarter choice. Still, proper installation is critical. Whether you choose fiber cement or vinyl, always work with certified contractors who know how to handle your region’s climate demands.
Ensure your siding investment delivers lasting performance. Work with certified professionals at My Modern Renovations for installation done right—backed by durable materials, clean workmanship, and attention to regional conditions. Schedule your consultation!
FAQs
Q1. How long does fiber cement siding last compared to vinyl siding? Fiber cement siding typically lasts 50-100 years with proper maintenance, while vinyl siding generally performs for 20-40 years. This significant difference in longevity is due to fiber cement's denser, more durable composition.
Q2. Is fiber cement siding more fire-resistant than vinyl siding? Yes, fiber cement siding is significantly more fire-resistant. It achieves the highest possible Class 1(A) fire spread rating and won't ignite or release toxic fumes during a fire. In contrast, vinyl siding melts when exposed to high heat and can contribute to flame spread.
Q3. How do installation costs compare between fiber cement and vinyl siding? Installation costs for fiber cement siding are generally higher, ranging from $4.00-$8.00 per square foot for labor, compared to $2.00-$5.00 per square foot for vinyl siding. This is due to fiber cement's weight and the specialized tools and expertise required for installation.
Q4. Which siding material is better for cold climates? Fiber cement siding is generally better for cold climates. It maintains its structural integrity during freeze-thaw cycles and resists cracking, shrinking, and swelling caused by freezing conditions. Vinyl can become brittle in extreme cold, making it more vulnerable to damage.
Q5. How does the choice of siding affect home value? According to recent data, fiber cement siding adds more value to a home compared to vinyl siding. Fiber cement siding can add approximately $17,129 to home value (88.5% ROI), while vinyl siding adds about $15,490. Additionally, fiber cement's fire resistance may lead to reduced insurance premiums.