Vinyl vs. Fiber Cement vs. Wood
Contents
During harsh winters, your West Virginia home's siding choice can significantly impact energy costs. In fact, brick siding reduces winter heat loss by 55%, while vinyl manages only 18%, and fiber cement about 11%. However, heat retention isn't the only factor to consider when selecting the best siding for cold climates. Durability, maintenance requirements, and overall cost-effectiveness play crucial roles in determining the ideal siding solution for your home.
While each siding material offers unique benefits, their performance varies dramatically in freezing conditions. Modern insulated vinyl siding improves home airtightness by 9.5% and reduces energy consumption by up to 8%. Meanwhile, fiber cement siding shows remarkable stability, maintaining its structure even after complete water saturation during freeze-thaw cycles, and can last over 50 years with minimal upkeep.
This guide examines how vinyl, fiber cement, and engineered wood siding materials perform in cold weather conditions, helping you make an informed decision for your WV home's protection, energy efficiency, and curb appeal.
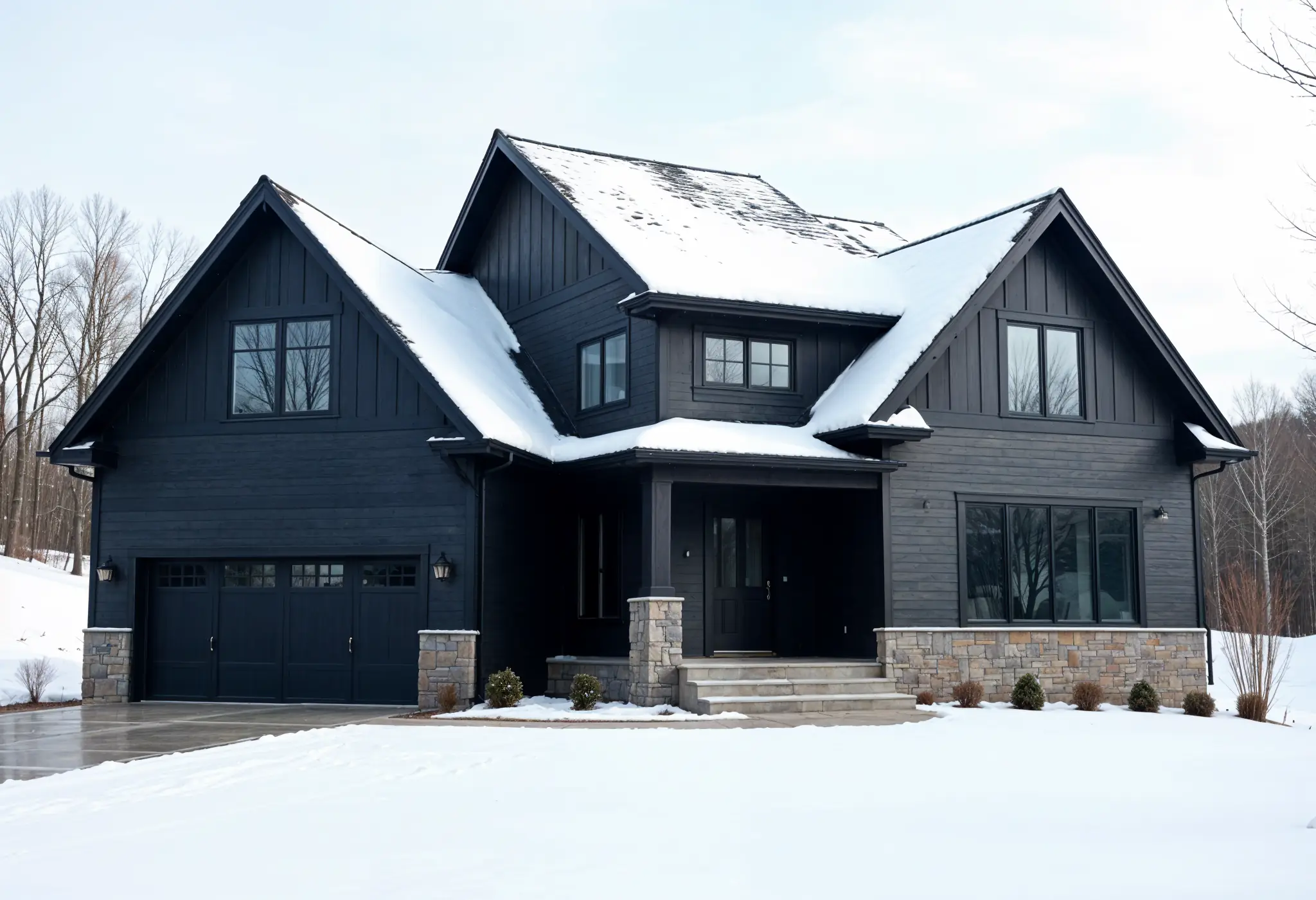
How Cold Weather Affects Different Siding Materials
Cold weather poses unique challenges to your home's exterior, with siding materials bearing the brunt of winter's assault. Understanding these challenges isn't just about aesthetics—it's about protecting your investment and ensuring your home remains structurally sound through seasons of freeze and thaw.
The science behind freeze-thaw cycles
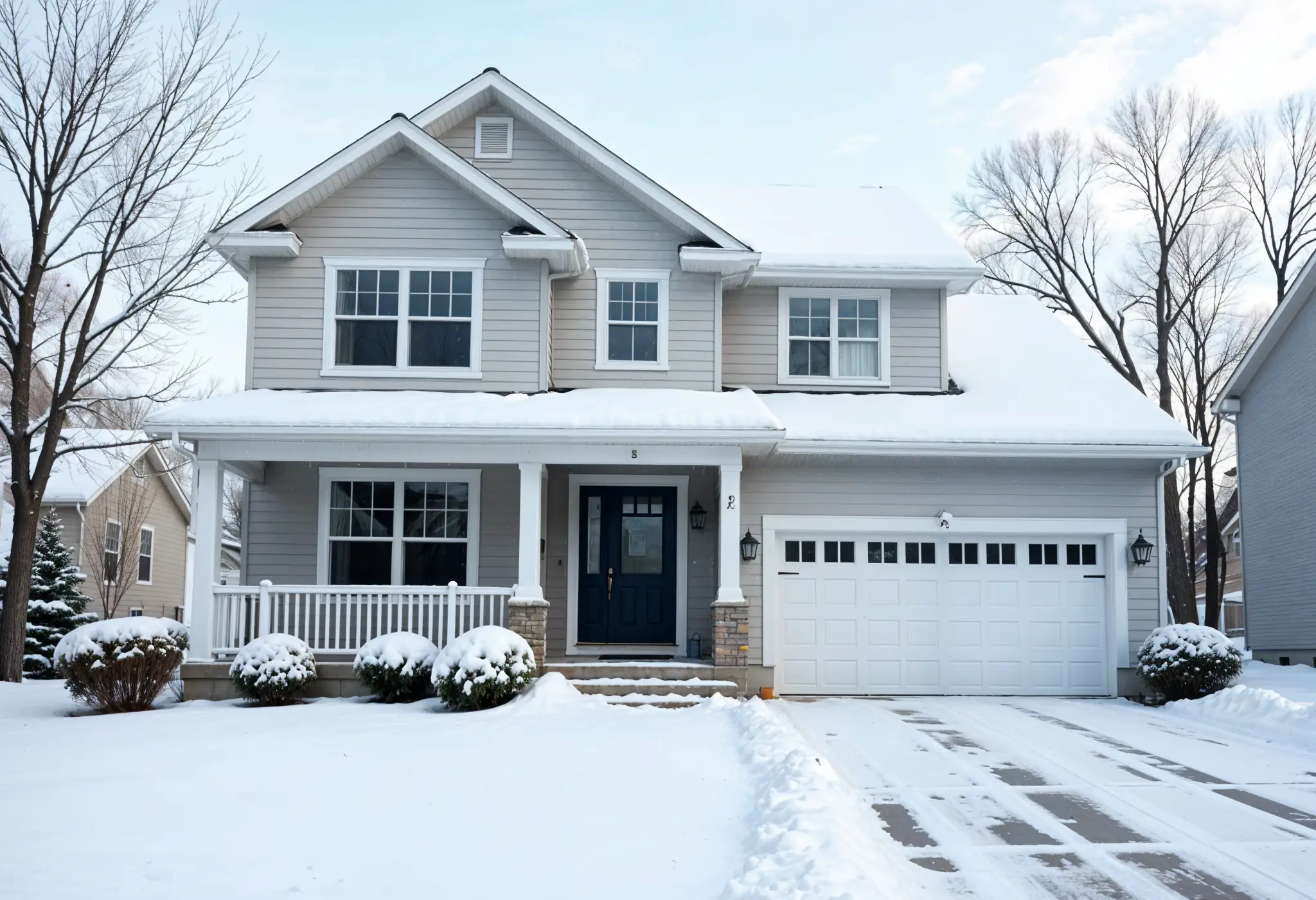
The freeze-thaw cycle is one of the most destructive forces impacting siding in cold climates. When temperatures swing above and below 32°F, water seeps into tiny cracks and pores in your home's siding, freezes at night, and expands by 9–10%, creating powerful internal pressure. This expansion widens cracks, and when the ice melts, more moisture penetrates deeper into the structure—setting off a cycle that can repeat hundreds of times each winter. Over time, these repeated freeze-thaw events cause significant siding damage, including cracking, warping, and splitting.
Cold-climate siding materials respond differently. Fiber cement siding—though concrete-based and naturally brittle—is engineered by brands like James Hardie to endure freeze-thaw cycles without breaking, even when wet. Vinyl siding flexes with temperature but becomes brittle in freezing weather, increasing the risk of cracks and panel failure. Wood siding is highly vulnerable unless regularly sealed and maintained; it absorbs moisture easily and deteriorates under repeated freezing. Engineered wood siding, however, combines treated wood fibers with strong binders to resist cracking and maintain strength despite extreme cold.
To assess siding for cold weather, manufacturers test moisture absorption and resistance under simulated freeze-thaw conditions—key to predicting long-term durability. Choosing siding built for cold climates can help you prevent structural issues, energy loss, and costly repairs over time.
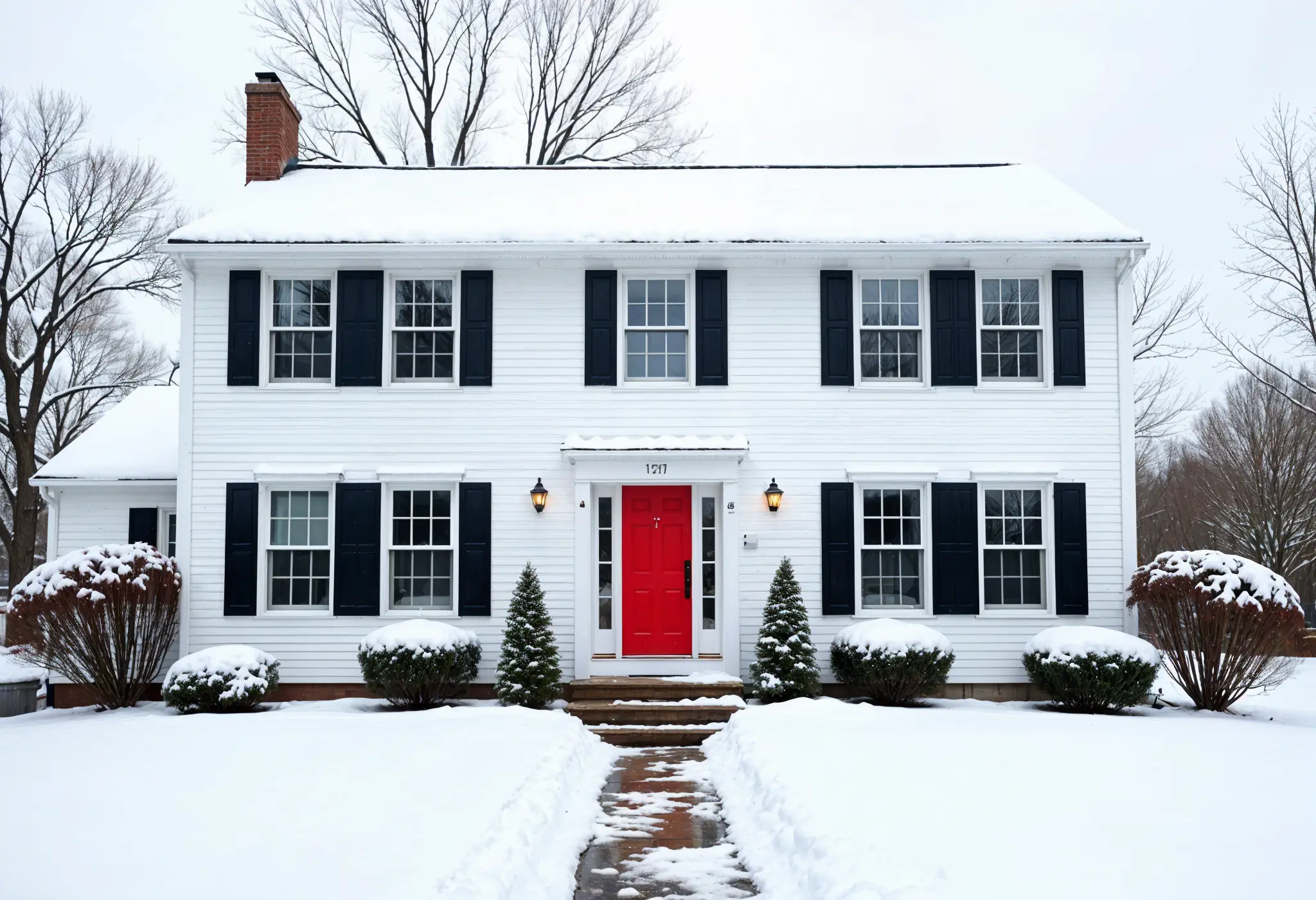
How Winter Moisture Affects Your Siding
Moisture represents the primary catalyst for winter siding damage, working in various ways to compromise your home's exterior protection. In cold climates, accumulated snow, ice, and freezing rain create perfect conditions for moisture to infiltrate siding materials.
The relationship between moisture and cold temperatures creates several distinct problems:
Moisture Infiltration Pathways: Winter storms can drive snow and ice against your home, causing it to stick to siding surfaces. As this precipitation melts, water seeps into any available cracks, gaps, or seams in the siding. Over time, this intrusion can damage both the siding itself and the underlying structure.
Seal Deterioration: The extreme cold combined with moisture can cause seals and caulking between siding panels and exterior walls to loosen, crack, or break. These compromised seals create new entry points for water, leading to accelerated deterioration.
Material-Specific Vulnerabilities: Each siding material responds differently to moisture exposure during winter:
- Vinyl siding generally resists moisture absorption but can still allow water to penetrate behind it if improperly installed or damaged. When temperatures fluctuate, this trapped moisture expands and contracts, potentially creating gaps that invite further water intrusion.
- Wood siding acts somewhat like a sponge, absorbing moisture that can lead to rot, particularly as protective layers wear away from snow and ice contact. This absorbed moisture expands when frozen, causing the wood to warp and crack over time.
- Fiber cement siding offers superior moisture resistance compared to traditional materials but isn't entirely immune. Excessive moisture absorption combined with freezing temperatures can potentially lead to swelling or warping if installation doesn't account for expansion and contraction. However, products like James Hardie's HZ5® line are specifically engineered to resist these issues in cold climates.
The effects of moisture intrusion impact more than just the exterior:
Mold and Mildew Development: When moisture infiltrates siding and underlying structures, it creates ideal conditions for mold and mildew growth. These fungi thrive in moist environments and can rapidly colonize affected areas, potentially causing health problems for residents and structural damage to building materials.
Rot Formation: Prolonged moisture exposure, particularly in wood siding and underlying wooden structures, leads to rot development. This decay progressively weakens affected materials, compromising their structural integrity and necessitating expensive repairs.
Insulation Damage: When winter storms loosen or damage siding, insulation may become exposed to moisture. Wet insulation loses much of its thermal resistance, increasing energy consumption and creating uncomfortable interior conditions.
Paint Degradation: Moisture trapped beneath siding can cause paint to bubble, peel, or separate from surfaces. This not only affects appearance but also eliminates a protective barrier against further moisture intrusion.
Structural Concerns: Perhaps most alarming, unchecked moisture penetration eventually reaches your home's structural elements. Water damage to framing, sheathing, and even foundation components can compromise your home's structural integrity, potentially leading to serious and costly repairs.
Early detection remains crucial for preventing extensive moisture damage. Signs to watch for include:
- Cracks in siding surfaces
- Loose or missing siding sections
- Peeling or bubbling paint
- Visible rot or mold growth
- Water stains on interior walls
- Unexplained increases in heating costs
Addressing these symptoms promptly can prevent minor issues from developing into major structural problems requiring extensive repairs.
Don’t let winter moisture destroy your West Virginia home from the outside in. From fiber cement to engineered wood, we install siding built to last through every snowstorm. Visit MyModernRenovations.com now for a free cold-climate siding consultation.
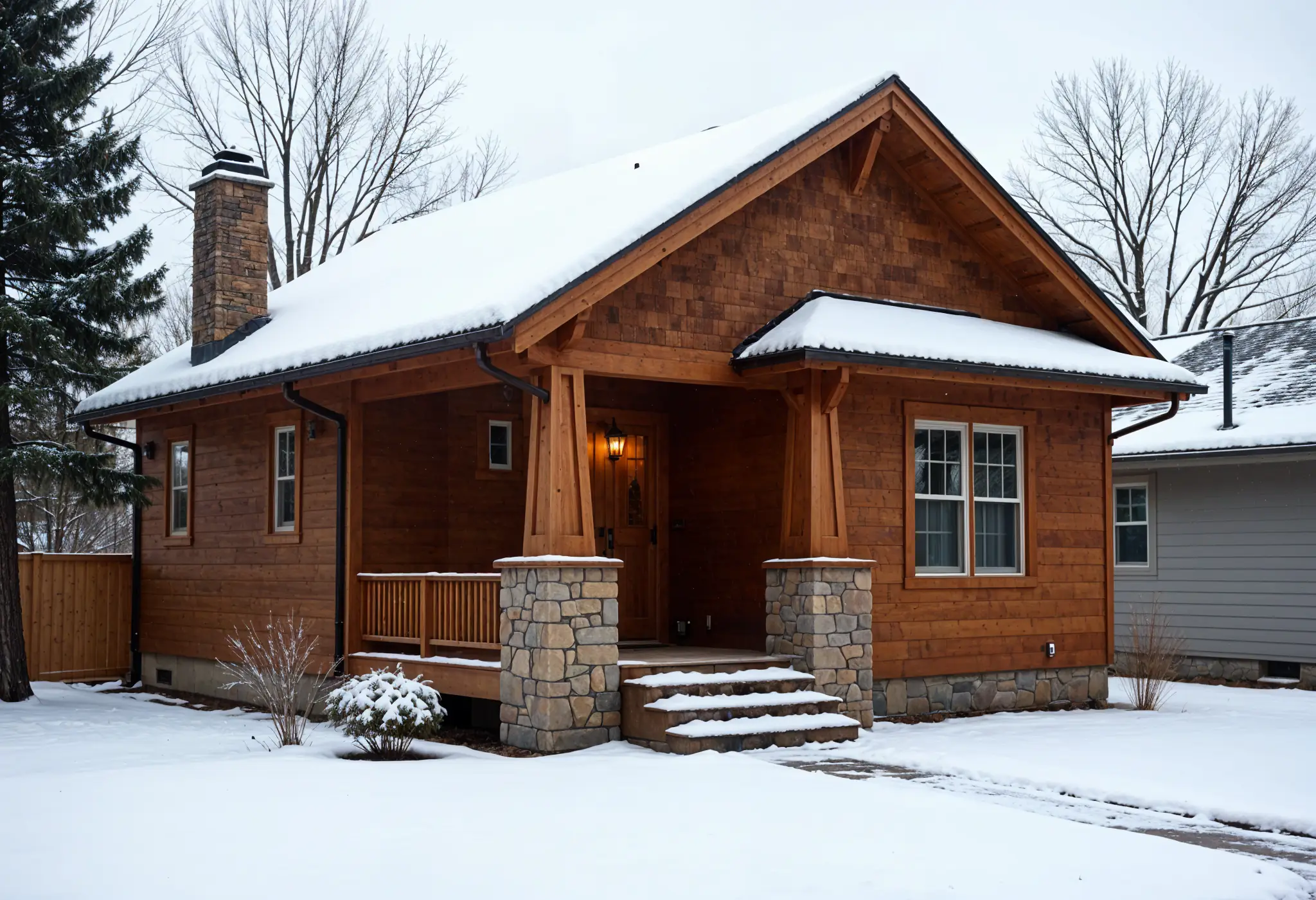
Wind and snow load considerations
Beyond temperature fluctuations and moisture concerns, cold-climate siding must withstand additional physical stresses from wind and snow accumulation. These forces create unique challenges that can compromise even well-maintained siding systems.
Wind Effects on Siding Integrity
Winter storms frequently bring intense winds that exert tremendous pressure on exterior surfaces. These winds can:
- Loosen or completely remove siding panels, particularly if materials are already weakened by age or previous damage.
- Drive snow, ice, and debris against siding surfaces at high velocities, potentially causing impacts that crack or dent panels. Vinyl siding becomes particularly vulnerable to impact damage during cold weather when its flexibility decreases.
- Create negative pressure zones that pull outward on siding sections, testing the strength of fasteners and attachment points. This "pulling" effect becomes more problematic when combined with the brittleness that affects many siding materials in cold temperatures.
- Accelerate heat loss through tiny gaps or cracks in siding systems, increasing energy consumption and interior discomfort.
For homes in particularly windy regions, choosing impact-resistant siding materials and ensuring professional installation with proper fastening techniques becomes especially important.
Snow Load Challenges
Snow accumulation creates both weight and moisture concerns for siding systems:
- Heavy snow buildup exerts downward pressure against siding, potentially causing warping, bending, or even structural damage if the siding is already compromised.
- Snow drifts that form against walls expose siding to prolonged contact with ice, moisture, and physical weight. This extended exposure increases the risk of water infiltration and material failure.
- Areas where snow regularly accumulates against siding experience more freeze-thaw cycles as snow melts and refreezes, accelerating the deterioration process.
- Melting snow can create unusual water intrusion patterns, sometimes allowing moisture to reach areas much higher on walls than typical rainfall would affect.
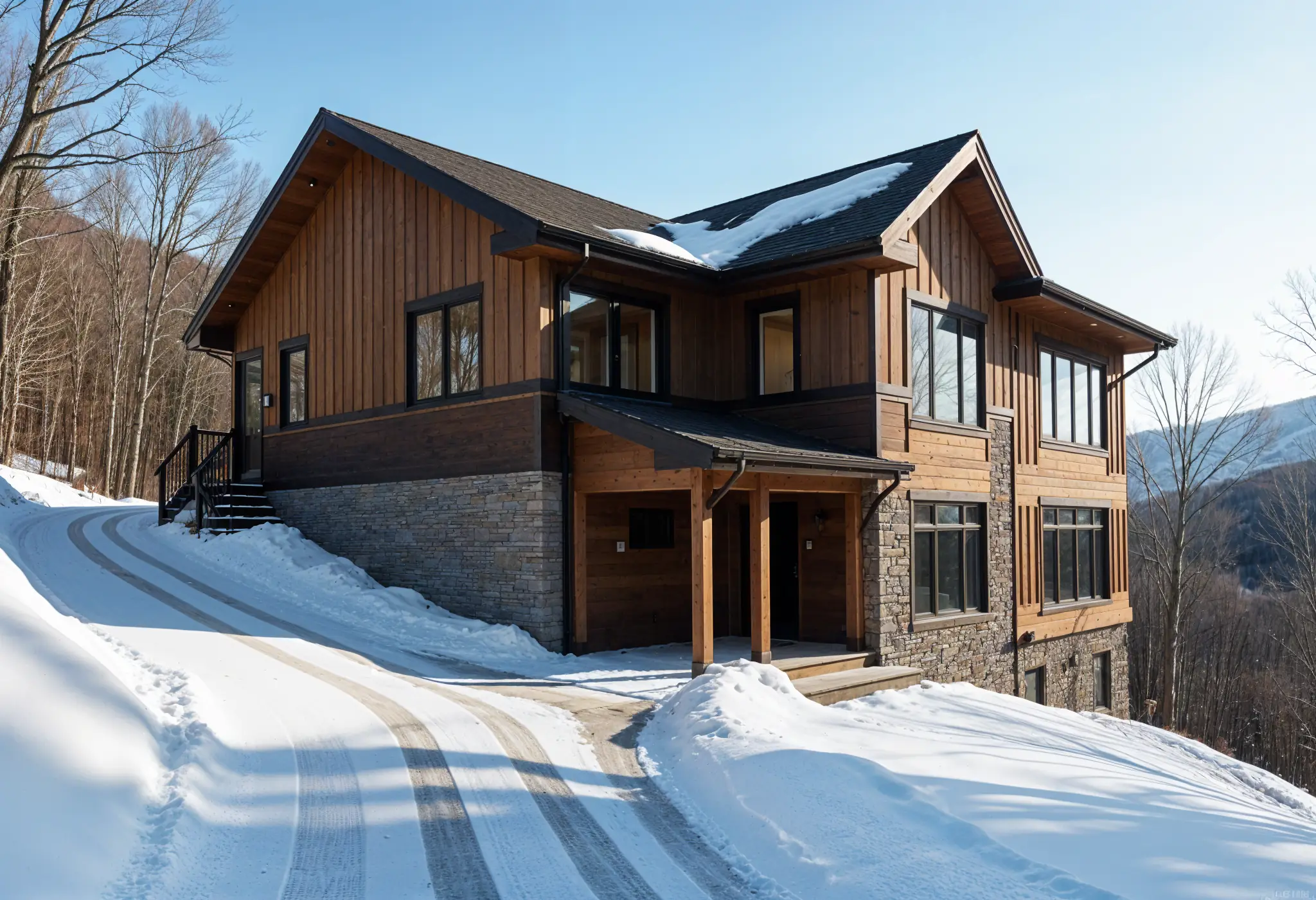
The way different siding materials respond to these snow-related challenges varies significantly:
Vinyl Siding Under Snow Load: Standard vinyl siding offers moderate resistance to snow accumulation but can become brittle in extreme cold. This brittleness increases susceptibility to cracking from the weight of heavy snow or from impacts during snow removal activities. Additionally, vinyl's expansion and contraction properties make it vulnerable to warping if snow melt repeatedly freezes and thaws against its surface.
Fiber Cement Performance: Fiber cement siding generally handles snow accumulation well due to its dimensional stability and moisture resistance. The HZ5® products from James Hardie, specifically designed for cold climates, retain their shape even under intense snow drifts and resist shrinking, swelling, and cracking despite years of exposure to wet and freezing conditions. This stability makes fiber cement an excellent choice for regions with heavy snowfall.
Wood Siding Challenges: Traditional wood siding faces particular challenges from snow loads. The combination of weight, moisture, and freeze-thaw cycles can accelerate deterioration, especially if protective finishes have begun to weather. Snow that melts against wood siding can penetrate the material, expanding when frozen and potentially causing splitting or warping.
Practical Snow Management
For homeowners in snow-prone regions, proper snow management becomes an essential aspect of siding protection:
- Use appropriate snow removal techniques near siding surfaces. Avoid using metal shovels directly against siding materials, opting instead for plastic shovels, brooms, or specialized snow rakes designed for building exteriors.
- Start snow removal from the top of the structure and work downward to prevent snow from falling and damaging lower siding sections.
- Maintain adequate clearance between snow piles and siding surfaces to minimize moisture contact and pressure against walls.
- Inspect shaded sides of the home regularly, as these areas experience slower melting and more prolonged snow contact, increasing the potential for frost damage.
Comprehensive Winter Protection
Protecting siding from winter's combined challenges requires a multi-faceted approach:
- Select siding materials specifically engineered for climate extremes. Products designated for cold climates, such as James Hardie's HZ5® line, incorporate features designed to withstand freeze-thaw cycles, moisture exposure, and temperature fluctuations.
- Ensure proper installation with appropriate gap allowances for expansion and contraction. For example, engineered wood siding typically requires a 3/16-inch gap between pieces to accommodate environmental changes without buckling or cracking.
- Apply weatherproof caulking around windows, doors, and other openings to prevent moisture intrusion, particularly before winter weather arrives.
- Maintain adequate ventilation in the attic and wall spaces to regulate temperature and humidity levels, reducing the risk of condensation within wall assemblies.
- Schedule professional inspections before and after winter seasons to identify and address potential issues before they escalate into major problems.
By understanding how cold weather affects different siding materials and taking appropriate preventative measures, you can significantly extend the lifespan of your home's exterior while maintaining its appearance and structural integrity throughout even the harshest winter conditions.
Comparing Vinyl, Fiber Cement, and Wood Siding Performance
When selecting siding for freezing environments, understanding how different materials perform under extreme conditions becomes crucial for making an informed decision. Let's examine how vinyl, fiber cement, and wood siding compare in terms of durability, performance, and insulation value in cold climates.
Vinyl siding: Flexibility vs. brittleness in freezing temperatures
Vinyl siding is a top choice for homeowners due to its affordability and low maintenance, but its cold climate performance has limitations. While vinyl’s flexibility allows it to expand and contract with temperature changes—reducing the risk of warping or buckling—it becomes brittle in extreme cold. Freeze-thaw cycles cause it to crack, especially during impacts from hail, snow, or ice. As vinyl contracts in freezing temperatures and expands during thawing, it can pull away from fasteners and create gaps that let in moisture.
This trapped water may freeze, expand, and damage siding further. Insulated vinyl siding offers better performance in cold climates by adding rigidity, impact resistance, and higher R-values, but it still faces challenges in prolonged sub-zero conditions. Proper cold-weather installation, with room for movement and secured fasteners, plus regular winter maintenance, can help extend vinyl’s durability. Ideal for moderate cold zones, vinyl siding needs extra care in harsh winters.
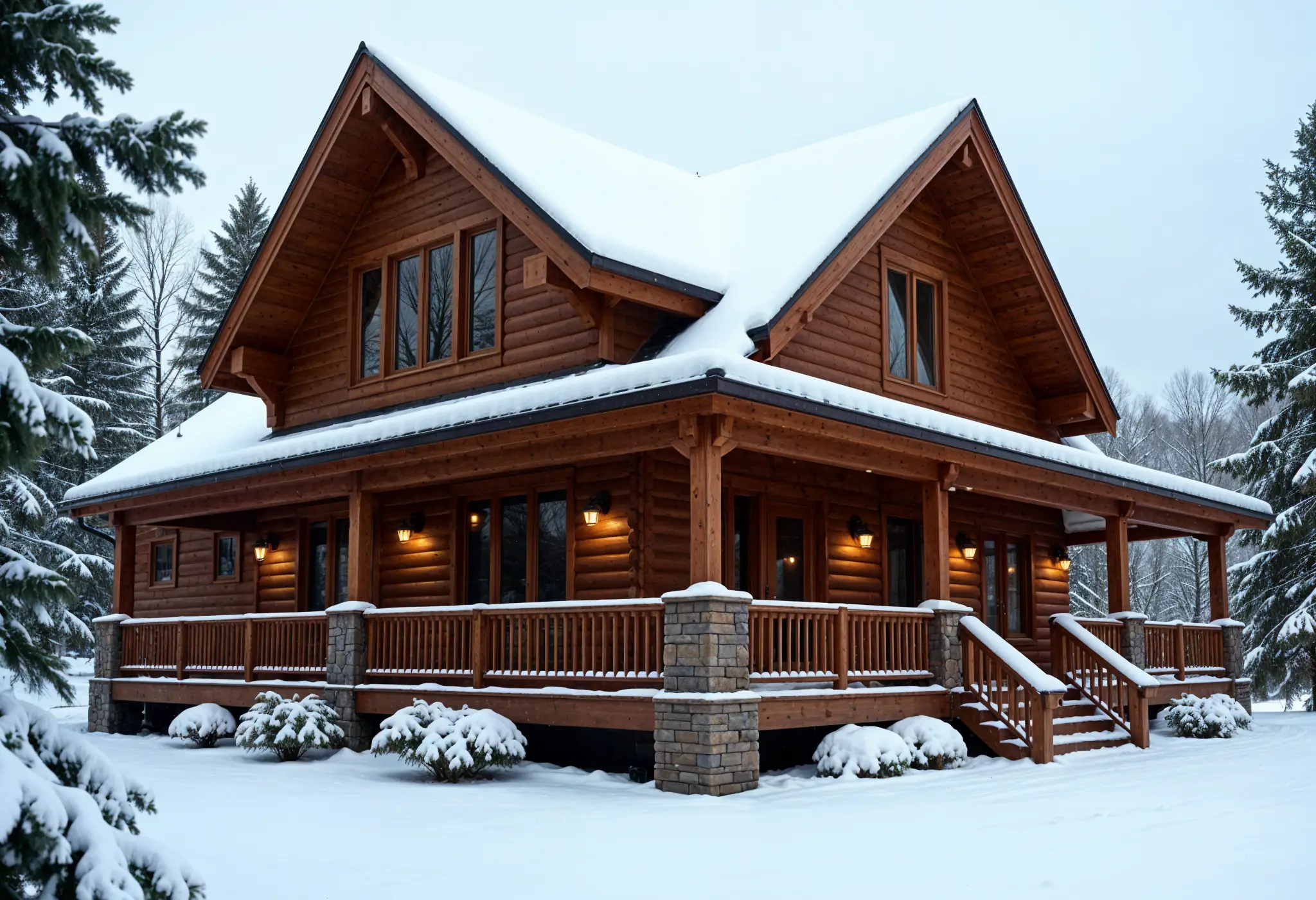
Fiber cement: Moisture resistance and dimensional stability
Fiber cement siding is a top-performing cold climate siding option, made from a durable mix of cement, sand, and cellulose fibers. Its biggest advantage is dimensional stability—unlike vinyl, it resists expansion, contraction, and warping during temperature swings. Fiber cement is also highly moisture-resistant, reducing the risk of freeze-thaw damage even when exposed to snow, ice, or heavy rain. Products like James Hardie’s HZ5® line are specifically engineered for cold, wet regions, with added protection against mold, cracking, and moisture intrusion. Unlike vinyl, fiber cement remains strong and non-brittle in freezing temperatures, and its non-combustible nature adds safety during heavy heating use. Ideal for freeze-thaw zones, its dense structure blocks water penetration and prevents siding failure over time. Though its R-value is modest (0.37–0.47), fiber cement can be combined with continuous insulation to boost energy efficiency. It requires professional installation, with proper spacing and flashing, to ensure long-term durability in extreme cold.
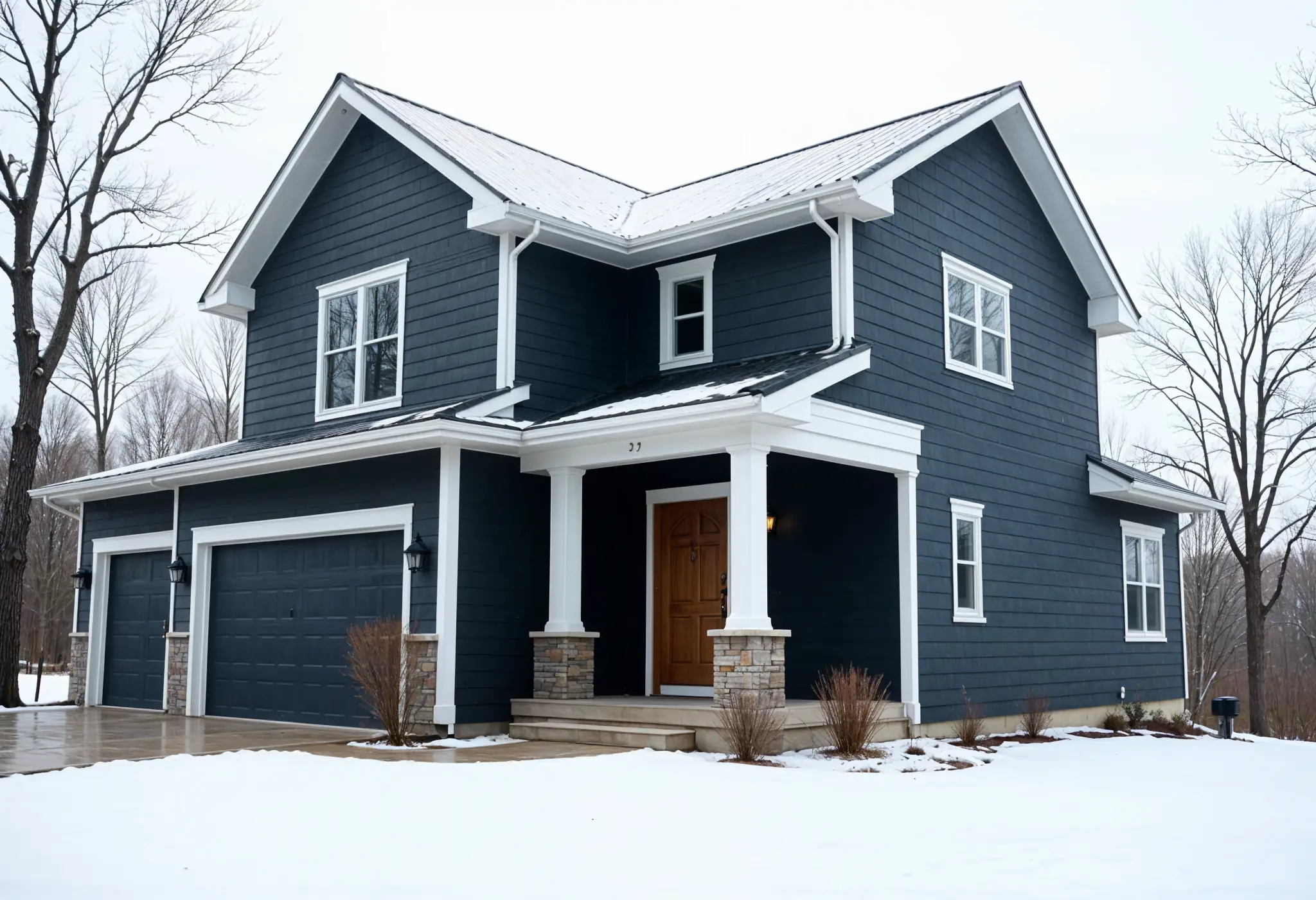
Wood siding: Natural insulation and weathering challenges
Wood siding offers timeless curb appeal and natural insulation, making it a popular choice for cold climates. Its cellular structure traps air, creating an effective thermal barrier that helps retain indoor heat during harsh winters. Western Red Cedar excels in freezing regions due to its natural oils that resist rot and its superior insulation value. Eastern White Pine and White Fir also perform well in cold, humid environments, with strong paint adhesion and weather resistance.
However, wood siding is more vulnerable to cold-weather damage than vinyl or fiber cement. It absorbs moisture, which expands when frozen, leading to warping, cracking, and potential rot during freeze-thaw cycles. Without regular sealing and painting, wood deteriorates over time, especially in areas exposed to snow and ice.
To enhance wood’s performance in freezing climates, proper installation gaps and a solid insulation layer beneath the siding are essential. Ongoing maintenance is critical to preserving both its look and structure. Engineered wood siding, modified using heat and steam, offers greater dimensional stability and better resistance to warping—ideal for cold-weather durability with a traditional wood aesthetic.
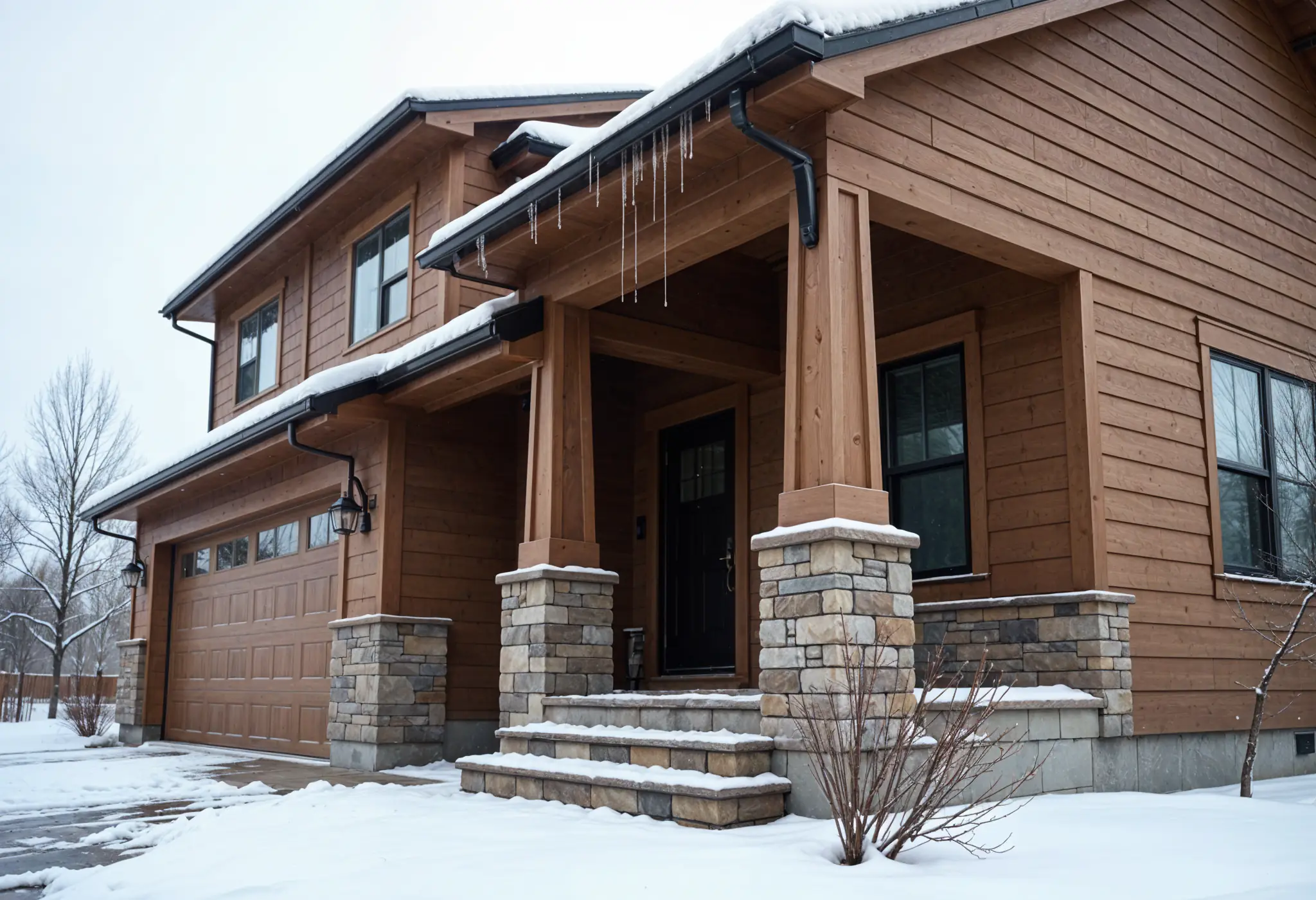
R-value comparison: Which provides the best insulation?
When evaluating siding materials for cold climates, R-value serves as a critical metric for determining insulation effectiveness. R-value measures a material's resistance to heat transfer—the higher the number, the better the insulation performance.
Among standard siding options, the R-value hierarchy reveals significant performance differences:
- Insulated Vinyl Siding: R-value of 3.5 to 5.0
- Traditional Wood Siding: R-value of 0.81 to 1.25
- Fiber Cement Siding: R-value of 0.37 to 0.47
- Traditional Vinyl Siding: R-value of approximately 0.61
Insulated vinyl siding delivers the highest R-value among popular cold-climate siding options, typically ranging from 3.5 to 5.0. Its built-in foam backing forms a continuous insulation layer, reducing thermal bridging and minimizing heat loss through walls. This makes insulated vinyl a top choice for energy-efficient homes in freezing temperatures. In comparison, standard wood siding offers moderate insulation (R-value 0.81–1.25), about twice that of traditional vinyl or fiber cement, thanks to its natural air-trapping cellular structure.
Fiber cement siding, while highly durable and moisture-resistant, has a low R-value (0.37–0.41), making it less effective as a standalone insulator. However, its dimensional stability and resistance to freeze-thaw damage provide consistent performance over time, making it a long-term energy-efficient solution in cold, wet climates. Pairing fiber cement or wood with continuous exterior insulation boards can drastically boost overall thermal efficiency.
James Hardie’s Lap Siding with Insulation offers an improved R-value of around 3.0, combining strength with enhanced energy savings. Even high-R siding can underperform if it cracks, warps, or allows air infiltration—common issues with vinyl due to temperature-driven expansion/contraction. Fiber cement resists air leaks, maintaining a tight thermal envelope. While insulated vinyl wins on raw R-value, fiber cement often delivers better real-world winter performance in extreme climates.
Long-Term Value: Durability and Maintenance in Cold Climates
Investing in the right siding material goes beyond immediate aesthetics—it's a long-term financial decision that affects your home's durability, maintenance requirements, and energy efficiency for decades to come. In cold climates, this decision becomes even more consequential as winter's harsh conditions test your home's exterior defenses.
Initial investment vs. lifetime costs
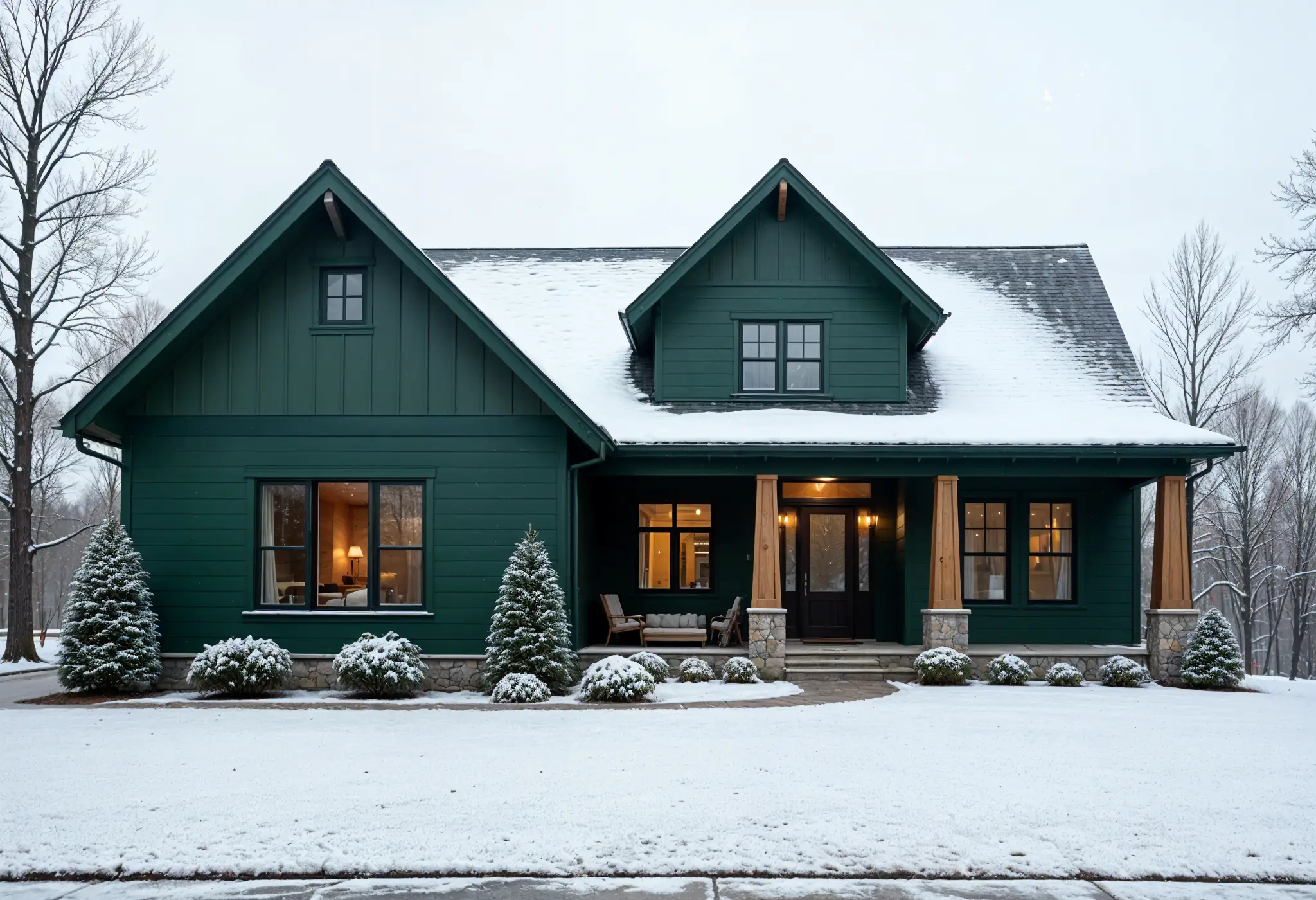
The initial price tag tells only part of the story when evaluating siding options for cold climates. Vinyl siding typically represents the most affordable upfront option, with insulated vinyl commanding a higher price point. Fiber cement sits in the mid-to-high range, whereas traditional wood offers varying price points depending on species and quality.
Looking beyond installation costs reveals a different financial picture, particularly in cold regions:
Vinyl siding generally requires replacement every 20-40 years, with standard vinyl potentially needing replacement sooner in areas with extreme temperature fluctuations. In contrast, fiber cement siding lasts 30-50 years with minimal maintenance, representing significant long-term savings despite higher initial costs.
Wood siding typically lasts 20-30 years but requires regular maintenance that adds to its lifetime cost. For cold-climate homes, this translates to more frequent repainting and sealing to protect against moisture penetration from snow and ice.
Most notably, fiber cement offers impressive return on investment—approximately 79% according to industry analysis, compared to 73% for standard vinyl and 72% for insulated vinyl. Throughout its lifespan, insulated vinyl provides additional value through reduced energy bills, potentially offsetting its higher initial cost.
Maintenance requirements during winter months
Winter care requirements vary significantly across siding materials, affecting both your maintenance schedule and long-term siding performance:
Vinyl siding demands relatively minimal winter maintenance, primarily requiring occasional checks for cracks or loose panels. Since vinyl becomes increasingly brittle as temperatures drop, avoid using metal shovels near siding surfaces and remove snow accumulation with plastic tools to prevent accidental damage.
Accordingly, fiber cement siding requires even less winter attention, maintaining its dimensional stability even during freeze-thaw cycles. Prior to winter, ensure all caulking around seams, windows and doors remains intact to prevent moisture infiltration.
Wood siding necessitates the most vigilant winter care. Regular inspections for water damage become crucial, as snow and ice exposure can lead to rot or warping. Signs like peeling paint often indicate water infiltration and require immediate attention to prevent structural damage from developing in frozen wood.
For all siding types, pre-winter inspection and maintenance prove fundamental to preventing costly mid-winter emergencies. Cleaning debris from gutters prevents water overflow onto siding, while sealing gaps and cracks before first frost prevents moisture intrusion that could freeze and expand.
Expected lifespan in harsh weather conditions
Cold-climate durability varies dramatically across siding materials:
Metal siding demonstrates exceptional longevity in cold environments, lasting 40-70 years with minimal maintenance. Its resistance to cracking in freezing temperatures makes it particularly valuable in regions with severe winters.
Fiber cement specifically engineered for cold regions, like James Hardie's HZ5® products, resists shrinking, swelling and cracking even after years of wet and freezing conditions. Standard fiber cement typically provides 30-50 years of service, maintaining its performance despite snow, ice, and temperature extremes.
In frigid environments, vinyl's lifespan often falls short of its potential. Although rated for 20-40 years, standard vinyl becomes brittle and crack-prone in extreme cold, potentially requiring earlier replacement in northern regions. Insulated vinyl performs better in this regard, with improved durability against both cold and impacts.
Wood siding, without meticulous maintenance, typically lasts 20-30 years before requiring replacement, with lifespan potentially shorter in areas experiencing frequent freeze-thaw cycles that accelerate deterioration.
Conclusion
Choosing the best siding for cold climates means balancing durability, insulation, maintenance, and budget. Fiber cement siding is the top performer—offering unmatched freeze-thaw resistance, 50-year lifespan, and minimal upkeep. Insulated vinyl siding provides strong thermal performance and affordability, making it ideal for moderately cold regions. Wood siding adds natural insulation and curb appeal but needs consistent maintenance to prevent moisture damage and rot.
For a balanced option, engineered wood siding like LP SmartSide delivers the charm of wood with better cold-weather durability. Climate-specific products like James Hardie’s HZ5® line are built to resist cracking, swelling, and mold in extreme conditions. Additionally, fiber cement and engineered wood offer eco-friendly siding benefits thanks to longer lifespans and recycled materials.
Get a free quote today and let our experts help you choose the perfect siding to protect and transform your home. Remember, investing in appropriate cold-climate siding now prevents costly repairs later while ensuring your home stays comfortable and energy-efficient through years of winter weather.
FAQs
Q1. What is the best siding material for homes in cold climates? Fiber cement siding is an excellent choice for cold climates due to its exceptional durability, dimensional stability, and resistance to moisture. It withstands freeze-thaw cycles without cracking or warping, making it highly reliable in harsh winter conditions. James Hardie's HZ5® line, specifically engineered for cold climates, offers superior performance in freezing temperatures.
Q2. How does vinyl siding perform in extremely cold temperatures? Vinyl siding becomes brittle and more susceptible to cracking in extremely cold temperatures. While it's an affordable option, its performance can be compromised in frigid conditions, potentially leading to damage from impacts or thermal stress. Insulated vinyl siding offers improved performance but still has limitations in severe cold.
Q3. What are the advantages of wood siding in cold regions? Wood siding offers natural insulation properties, helping to maintain interior warmth during harsh winters. Certain wood species, like Western Red Cedar, provide excellent resistance to rot and decay. However, wood requires more frequent maintenance compared to other siding materials. Engineered wood siding, such as LP SmartSide, offers improved durability and rot resistance while maintaining the aesthetic appeal of wood.
Q4. How does fiber cement siding compare to other materials in terms of insulation? While fiber cement siding itself has a relatively low R-value, it can be paired with additional insulation to create a highly effective thermal barrier. Its dimensional stability and moisture resistance contribute to consistent long-term thermal performance in cold climates. James Hardie offers insulated fiber cement options that provide improved R-values while maintaining the material's durability.
Q5. What maintenance is required for different siding materials in winter? Vinyl siding requires minimal winter maintenance beyond occasional checks for cracks. Fiber cement needs little attention, mainly ensuring intact caulking around seams and openings. Wood siding demands the most vigilant care, including regular inspections for water damage and potential repainting or resealing to prevent moisture infiltration. Engineered wood siding typically requires less maintenance than traditional wood but still benefits from regular inspections and upkeep.